Some background: One of the products made by our company was designed almost 50 years ago. Needless to say, the original engineers are long gone, and downsizing over the years has eliminated almost all of those positions. One of their legacies is a stainless steel part spec that we're wondering about, and I'm just a lowly EE, so this is way out of my field.
Material description is: CR Stainless Steel, 0.004" thick; Temper: Full Hard; Hardness: VHN452 (C 46); Ultimate Tensile Strength: 203,000/205,000 PSI. Mat'l Specs: AMS-5906B, AMS-5913B, ASTM-A-666-15. The part is a flat spiral spring, acid etched, 0.995" dia., appearance very similar to the image below:
The problem is that the spec calls for stress relieving, 3 hours at 600F, air cooling. The supplier has tried this using the full 12" strip size, before etching, and has extremely low yield of the finished parts due to warping of the strip.
Our questions are: 1) What benefit, if any, is derived from stress relieving this part; and 2) If it is beneficial, should stress relief be done before etching, or after? (My novice brain tells me "after", but what do I know?) The springs are constantly subjected to axial deflection up to +/- 0.100" and temperature up to 500F in the final assemblies, if that affects the answers.
Thanks in advance for any guidance.
-Brian
Material description is: CR Stainless Steel, 0.004" thick; Temper: Full Hard; Hardness: VHN452 (C 46); Ultimate Tensile Strength: 203,000/205,000 PSI. Mat'l Specs: AMS-5906B, AMS-5913B, ASTM-A-666-15. The part is a flat spiral spring, acid etched, 0.995" dia., appearance very similar to the image below:
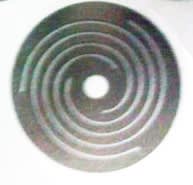
The problem is that the spec calls for stress relieving, 3 hours at 600F, air cooling. The supplier has tried this using the full 12" strip size, before etching, and has extremely low yield of the finished parts due to warping of the strip.
Our questions are: 1) What benefit, if any, is derived from stress relieving this part; and 2) If it is beneficial, should stress relief be done before etching, or after? (My novice brain tells me "after", but what do I know?) The springs are constantly subjected to axial deflection up to +/- 0.100" and temperature up to 500F in the final assemblies, if that affects the answers.
Thanks in advance for any guidance.
-Brian