Logan82
Structural
- May 5, 2021
- 212
Hi!
Many strut and tie models in publications are not stable trusses (the members don't necessarily form triangles), yet they are accepted as is. I was wondering why?
For example, in the first picture, from ACI 318 chapter 23, the truss seems to be missing a member. I was wondering why this member was not modeled?
I have added a member here to show what I mean:
Many strut and tie models in publications are not stable trusses (the members don't necessarily form triangles), yet they are accepted as is. I was wondering why?
For example, in the first picture, from ACI 318 chapter 23, the truss seems to be missing a member. I was wondering why this member was not modeled?
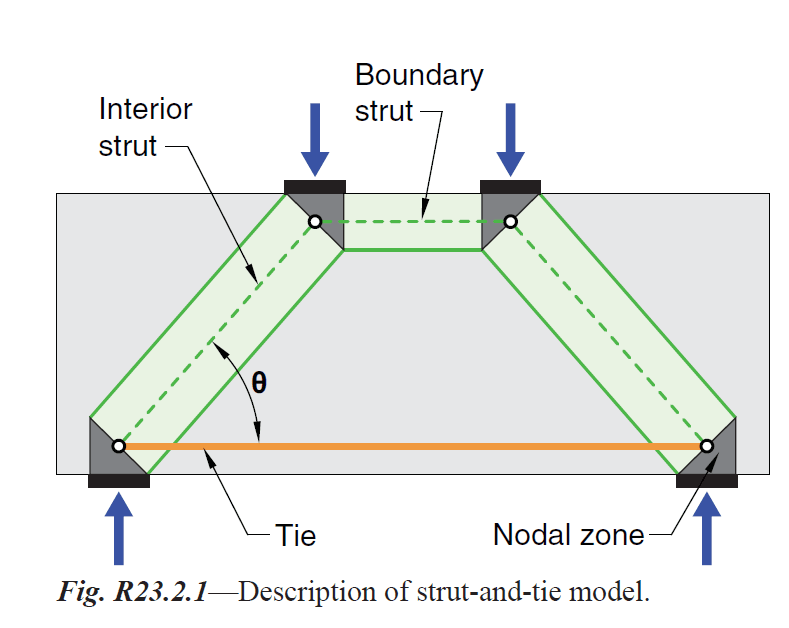
I have added a member here to show what I mean:
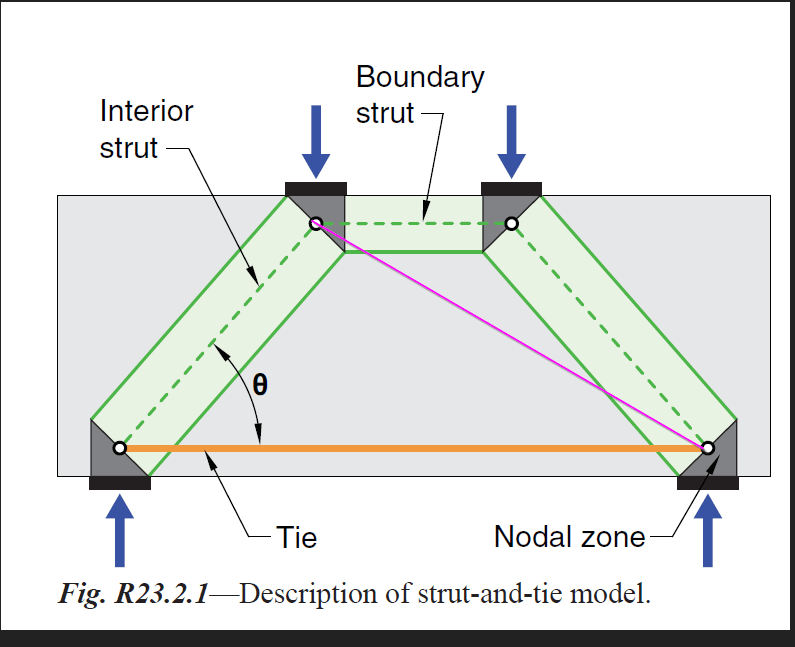