I want to enquire about the requirements of using headed bars for anchoring reinforcement of tension pile in pile cap. The tension force is in the order of about 4.3MN in ULS and 6B40+4B32 pile bars are anchored in the pile cap to take up this force. Though not ideal, the headed bars are placed below the top mat of pile cap to avoid clashes. To check the detailing arrangement, a local STM is developed and additional transverse links is provided around the pile reinforcement within the pile cap depth.
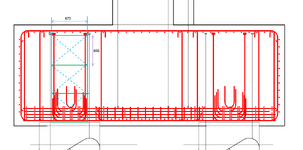
Additionally, the shear links (12 or 16mm dia) within the pile cap is anchored at bottom (B1 layer) using headed bars. This was done for easy placement of the links at site. Are there any additional requirements for the shear anchorage of headed bars apart from the ones stated in 25.4.4.1 & 25.4.4.2 of ACI 318-19.
I am curious to know whether the approach followed for detailing is reasonable and as to what others have done in similar situations. Thank you very much!
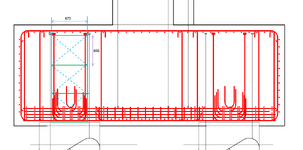
Additionally, the shear links (12 or 16mm dia) within the pile cap is anchored at bottom (B1 layer) using headed bars. This was done for easy placement of the links at site. Are there any additional requirements for the shear anchorage of headed bars apart from the ones stated in 25.4.4.1 & 25.4.4.2 of ACI 318-19.
I am curious to know whether the approach followed for detailing is reasonable and as to what others have done in similar situations. Thank you very much!