Quade999
Civil/Environmental
- May 29, 2020
- 61
Hi Everyone,
When using high strength steel reinforcing bars (100ksi yield strength), the compression splice length will actually be larger than the tension splice length. My question is, if I have a situation like shown below, where the region of a slab will cycle through positive and negative moment depending on where the moving load is positioned, is it ok to design the splice for the tension yield provided that any benefit of the reinforcement in compression is ignored in analysis? Normally when high strength steel is used (100ksi), we assume reinforcement is 60ksi for the design of all components, including splices and development. With 60ksi reinforcement, tension development length will almost always govern.
Thanks
When using high strength steel reinforcing bars (100ksi yield strength), the compression splice length will actually be larger than the tension splice length. My question is, if I have a situation like shown below, where the region of a slab will cycle through positive and negative moment depending on where the moving load is positioned, is it ok to design the splice for the tension yield provided that any benefit of the reinforcement in compression is ignored in analysis? Normally when high strength steel is used (100ksi), we assume reinforcement is 60ksi for the design of all components, including splices and development. With 60ksi reinforcement, tension development length will almost always govern.
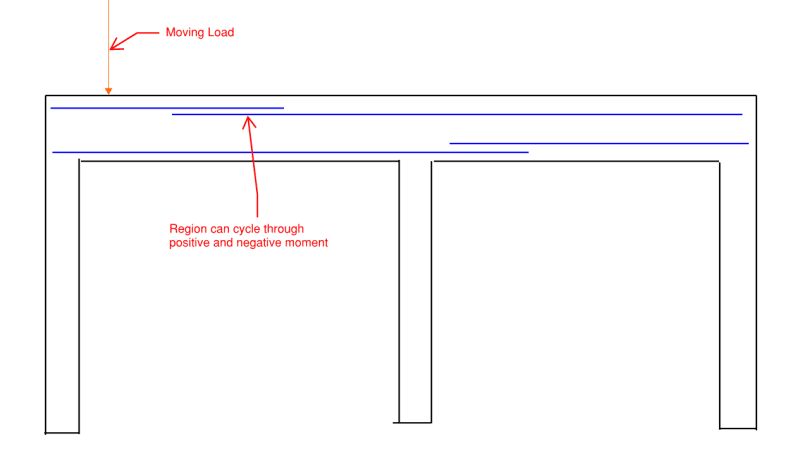
Thanks