-
1
- #1
milkshakelake
Structural
I'll make the case for a paperless office workflow!
I've been using this setup for 2 years and haven't looked back. All of this hinges on having a display tablet, not to be confused with a regular drawing tablet because those suck. To be clear, I don't advocate paperless outside the office; I still use pen and paper for site visits and meetings. I'm also not describing a note taking device; that's covered in detail in the threads below, but can easily complement the workflow I'm presenting. Feel free to poke holes in any of this! It's just for fun.
There have been a few threads on the subject:
1. You get a clean workspace, which increases clarity of mind and productivity
This is my home office. Real office is similar, but with more monitors. I didn't clean it up; this is in the middle of work. Enough space for my protein shake, super cool rock, and cold water. Display tablet is on the right.
Before I went paperless and was working for someone else, the office looked something like this. It's not an exaggeration; the reality was worse. There were also bookcases, shelves, and repurposed furniture just to hold drawings and binders.
2. You don't have to look through millions of pieces of paper to find a calculation
Calculations are organized into electronic folders. It beats walking to a bookcase, finding the right binder, and flipping to the right page of calculations.
3. With a tablet display and Excel, it's faster and easier to make calculations
Instead of printing and annotating an engineering drawing for a calculation, you could take a screenshot and mark it up. This works seamlessly in Excel, which has built-in drawing tools.
You can incorporate markups like you would with paper calculations, along with math. Some advantages over paper include being able to easily modify numbers (and have them propagate through calculations), move things around like sketches, and work on an infinite canvas. Should you need it, you also have the power of VBA programming at your fingertips. This is better than paper.
I didn't make any attempt to make these look nice or easy to follow. But should it need to be submitted to an official, it can be made to look more professional. It's the same thing with paper.
4. You can incorporate results from other programs in the same file
This one is not a 100% slam dunk. Microsoft Office isn't quite there yet when it comes to integrating Word, Excel, and PDFs. But it is possible, though quite janky. But on paper? You have to print out the results and lose the order. In Excel, you can paste a PDF on a separate sheet, even multiple sheets, and it will retain the order. I've done 60 page long calculations by doing this in one Excel file. (If you're using SMath or something else, this argument falls apart a bit.)
5. Sketches? Yeaa boii
Some engineers like to have a notebook full of sketches, calculations, and random thoughts. Use OneNote or Krita. OneNote can save stuff in a hierarchical fashion and have different workbooks, chapters, and sheets. I personally don't work like this and I save everything to a specific place, but I created a quick notebook to demonstrate this.
As a plus, you can take a screenshot of anything you want to mark up, like a dimension or changes to a detail, and shoot it off to a client or coworker or employee. I have one remote drafter and 100% of our communications are done with paperless markups on pdf's. So the advantages go well and far beyond calculations. The caveat is with engineering drawings, even with a big display, you have to zoom in and out quite a bit. My work office has a fancier display tablet with programmable knobs and controls for that, which makes it less onerous.
6. You can carry your calculations everywhere
This is definitely not possible with paper, unless you scan and organize everything. I have my server hooked up to a Onedrive and Goodsync cloud mirror, which I can access with my phone. I can pull up Excel calculations and pdf's anywhere I go. It's been useful in a few cases where I was at a meeting and didn't have a certain calculation or drawing on hand, and didn't have to call back to the office to have it sent. It takes some practice and getting used to, but it doubles as a neat trick in a meeting.
Now, to address concerns!
Doesn't feel as good as paper
I agree, but it's pretty damn close. An engineer I know was forced to use a display tablet over a decade ago and she hated it. She tried my display and said it's so good, it's like night and day. The technology is refined, and will only get better.
It's not precise and/or it's clumsy
That's because your tablet is too small! I use a 24" tablet with 2K resolution. I tried Microsoft Surface and iPad, and those are too small to use effectively. I do NOT recommend going the laptop or handheld tablet route; I need a beastly, non-portable monster tablet. With a big enough display, you don't have to zoom in and out. If you have the desk space and budget, I recommend going even bigger. (It's just my two cents; some people have had success with laptops.)
Use paper and scan it!
Nah, this is superior. It saves the step where you print something out, mark it up, go back to scan it, and save it in the right place. Those seconds add up. Plus, electronically, everything has an infinite canvas and things can be moved around.
I don't want to pay for subscriptions!
Microsoft Office is the only subscription service used here that's different from a paper setup. Cloud services for carrying your calculations around are optional, and it can be self hosted with free open source apps like Nextcloud (it's a bit more advanced and needs Linux).
I've been using this setup for 2 years and haven't looked back. All of this hinges on having a display tablet, not to be confused with a regular drawing tablet because those suck. To be clear, I don't advocate paperless outside the office; I still use pen and paper for site visits and meetings. I'm also not describing a note taking device; that's covered in detail in the threads below, but can easily complement the workflow I'm presenting. Feel free to poke holes in any of this! It's just for fun.
There have been a few threads on the subject:
1. You get a clean workspace, which increases clarity of mind and productivity
This is my home office. Real office is similar, but with more monitors. I didn't clean it up; this is in the middle of work. Enough space for my protein shake, super cool rock, and cold water. Display tablet is on the right.
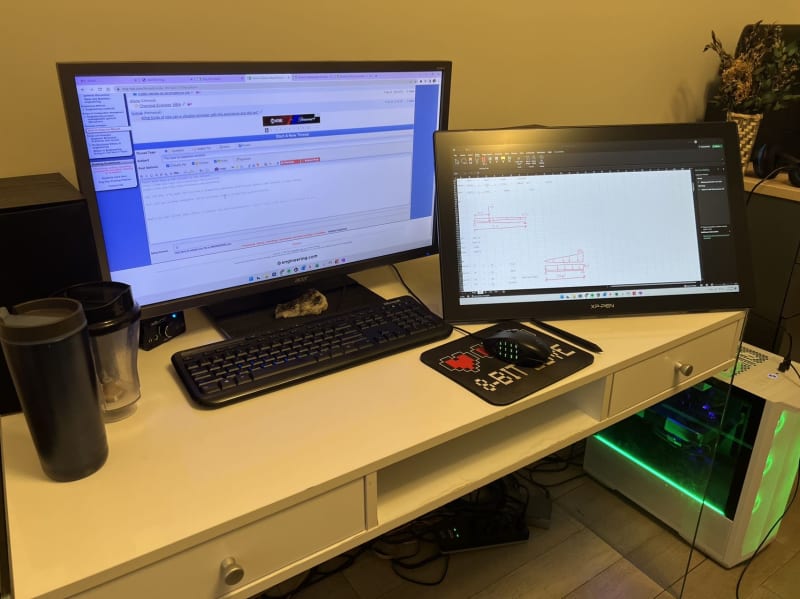
Before I went paperless and was working for someone else, the office looked something like this. It's not an exaggeration; the reality was worse. There were also bookcases, shelves, and repurposed furniture just to hold drawings and binders.
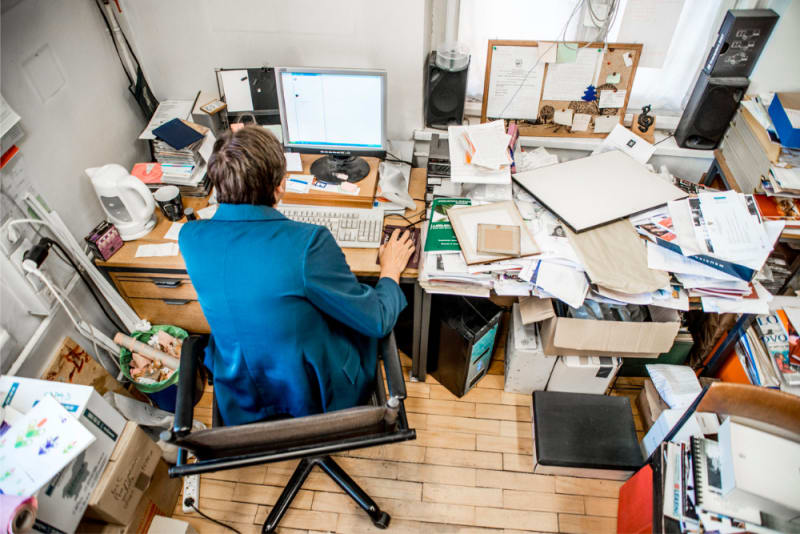
2. You don't have to look through millions of pieces of paper to find a calculation
Calculations are organized into electronic folders. It beats walking to a bookcase, finding the right binder, and flipping to the right page of calculations.
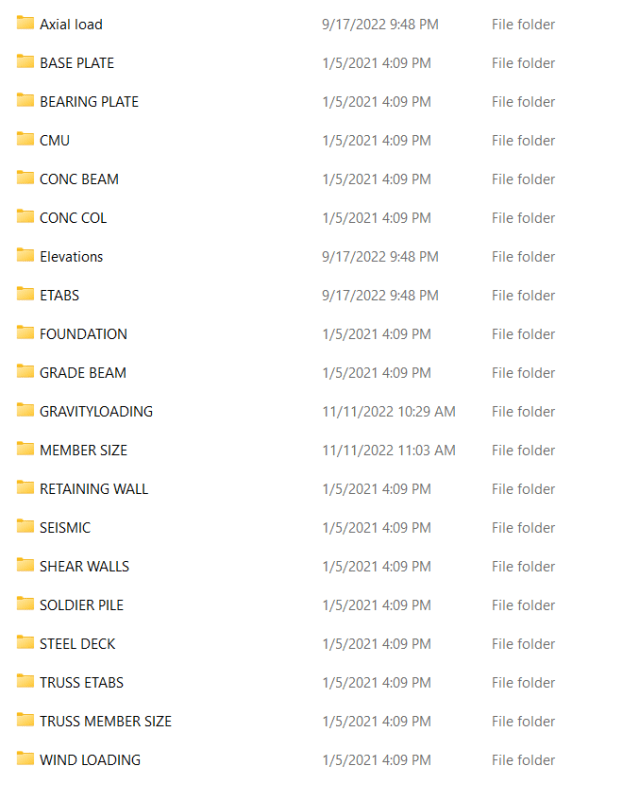
3. With a tablet display and Excel, it's faster and easier to make calculations
Instead of printing and annotating an engineering drawing for a calculation, you could take a screenshot and mark it up. This works seamlessly in Excel, which has built-in drawing tools.
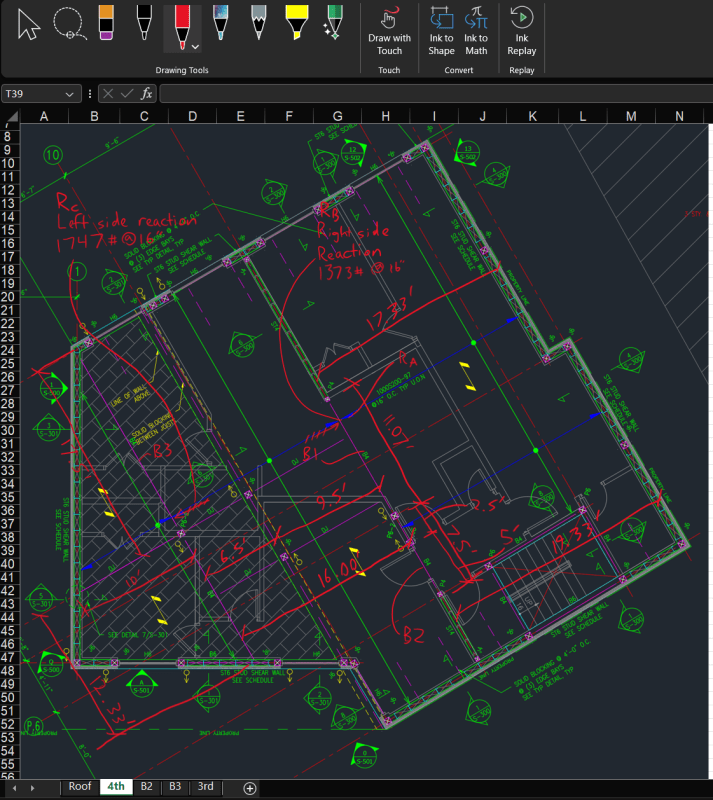
You can incorporate markups like you would with paper calculations, along with math. Some advantages over paper include being able to easily modify numbers (and have them propagate through calculations), move things around like sketches, and work on an infinite canvas. Should you need it, you also have the power of VBA programming at your fingertips. This is better than paper.
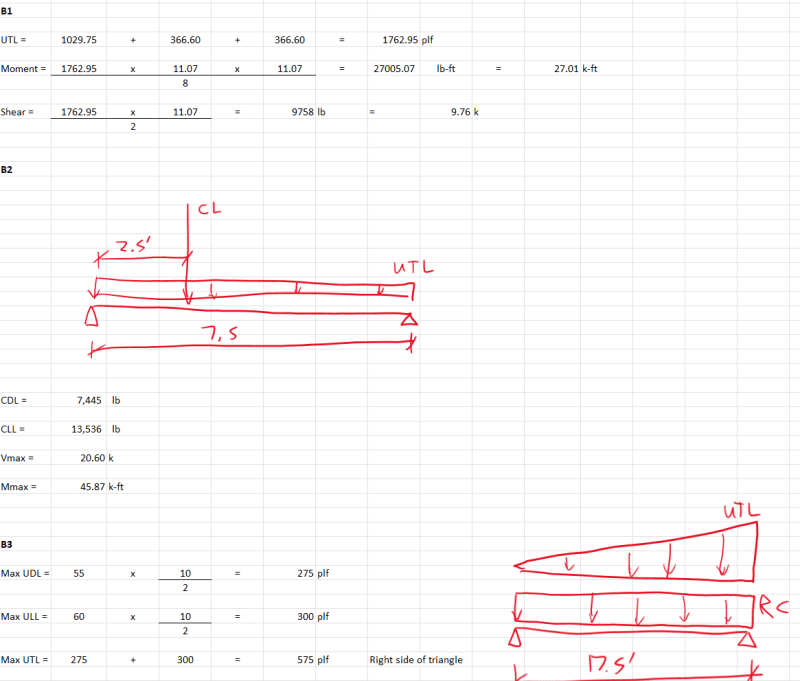
I didn't make any attempt to make these look nice or easy to follow. But should it need to be submitted to an official, it can be made to look more professional. It's the same thing with paper.
4. You can incorporate results from other programs in the same file
This one is not a 100% slam dunk. Microsoft Office isn't quite there yet when it comes to integrating Word, Excel, and PDFs. But it is possible, though quite janky. But on paper? You have to print out the results and lose the order. In Excel, you can paste a PDF on a separate sheet, even multiple sheets, and it will retain the order. I've done 60 page long calculations by doing this in one Excel file. (If you're using SMath or something else, this argument falls apart a bit.)
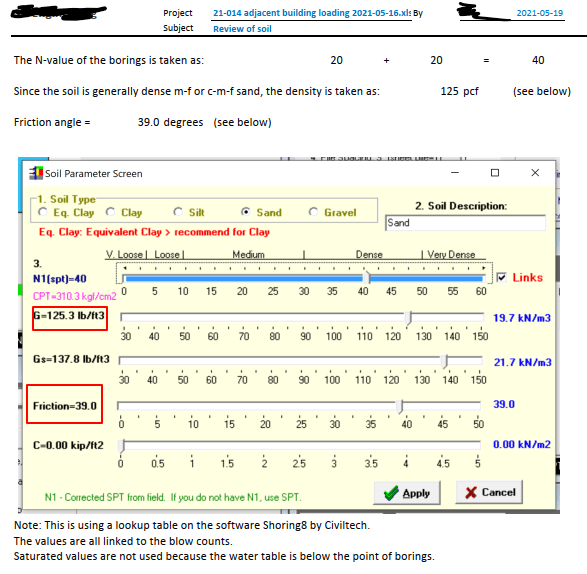
5. Sketches? Yeaa boii
Some engineers like to have a notebook full of sketches, calculations, and random thoughts. Use OneNote or Krita. OneNote can save stuff in a hierarchical fashion and have different workbooks, chapters, and sheets. I personally don't work like this and I save everything to a specific place, but I created a quick notebook to demonstrate this.
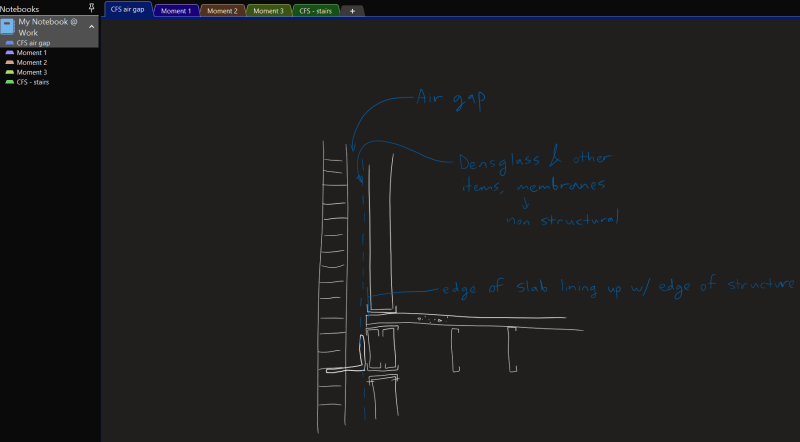
As a plus, you can take a screenshot of anything you want to mark up, like a dimension or changes to a detail, and shoot it off to a client or coworker or employee. I have one remote drafter and 100% of our communications are done with paperless markups on pdf's. So the advantages go well and far beyond calculations. The caveat is with engineering drawings, even with a big display, you have to zoom in and out quite a bit. My work office has a fancier display tablet with programmable knobs and controls for that, which makes it less onerous.
6. You can carry your calculations everywhere
This is definitely not possible with paper, unless you scan and organize everything. I have my server hooked up to a Onedrive and Goodsync cloud mirror, which I can access with my phone. I can pull up Excel calculations and pdf's anywhere I go. It's been useful in a few cases where I was at a meeting and didn't have a certain calculation or drawing on hand, and didn't have to call back to the office to have it sent. It takes some practice and getting used to, but it doubles as a neat trick in a meeting.
Now, to address concerns!
Doesn't feel as good as paper
I agree, but it's pretty damn close. An engineer I know was forced to use a display tablet over a decade ago and she hated it. She tried my display and said it's so good, it's like night and day. The technology is refined, and will only get better.
It's not precise and/or it's clumsy
That's because your tablet is too small! I use a 24" tablet with 2K resolution. I tried Microsoft Surface and iPad, and those are too small to use effectively. I do NOT recommend going the laptop or handheld tablet route; I need a beastly, non-portable monster tablet. With a big enough display, you don't have to zoom in and out. If you have the desk space and budget, I recommend going even bigger. (It's just my two cents; some people have had success with laptops.)
Use paper and scan it!
Nah, this is superior. It saves the step where you print something out, mark it up, go back to scan it, and save it in the right place. Those seconds add up. Plus, electronically, everything has an infinite canvas and things can be moved around.
I don't want to pay for subscriptions!
Microsoft Office is the only subscription service used here that's different from a paper setup. Cloud services for carrying your calculations around are optional, and it can be self hosted with free open source apps like Nextcloud (it's a bit more advanced and needs Linux).