Benjamin Blackford
Mechanical
- Jul 7, 2017
- 7
Hi all,
I'm relatively new to ansys apdl, and am having a lot of trouble with contact analysis in APDL Mechanical. I'm not able to correctly transfer temperatures between two bodies with contact elements in between them. I've attached an image of the problem, and also the txt file that I'm using. Unfortunately I need to use txt import, and not the gui or workbench. Any help you're able to give is really appreciated, as I've been struggling with this for weeks.
I'm relatively new to ansys apdl, and am having a lot of trouble with contact analysis in APDL Mechanical. I'm not able to correctly transfer temperatures between two bodies with contact elements in between them. I've attached an image of the problem, and also the txt file that I'm using. Unfortunately I need to use txt import, and not the gui or workbench. Any help you're able to give is really appreciated, as I've been struggling with this for weeks.
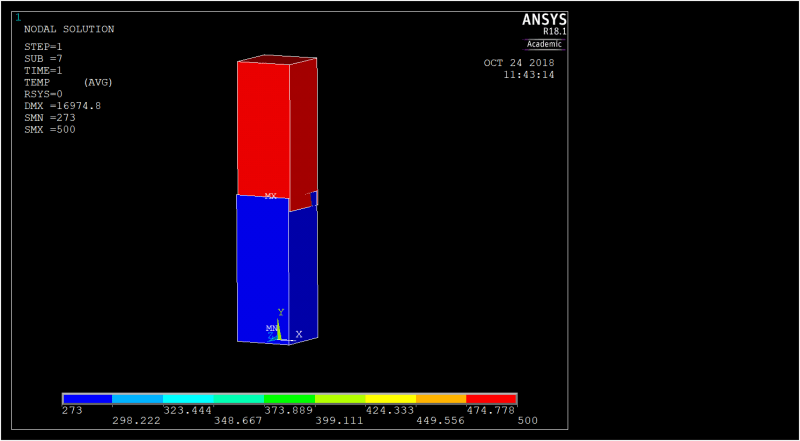