Marcin Wysocki
Computer
How to analyze nozzle loads for two plate heat exchangers arranged as in the image below? How to interpret large forces along the pipeline axis resulting from thermals? such systems are commonly used and are not damaged.
I assume that obtaining nozzle stiffness values from the manufacturer will not be an easy task, and in some cases, it may even be impossible.
...but I assume that the axial stiffness (especially of the lower cooler connections) is very high.The axial thermal forces calculated by Autopipe on these connections will be enormous, and it may be impossible to meet for e.g. the API standard.
As I mentioned above, systems of this type operate in many installations wihout damage or failure. I am wondering how to prepare a nozzles load analysis in a way that will allow to meet the standard e.g. API 662.
Regards
Marcin Wysocki
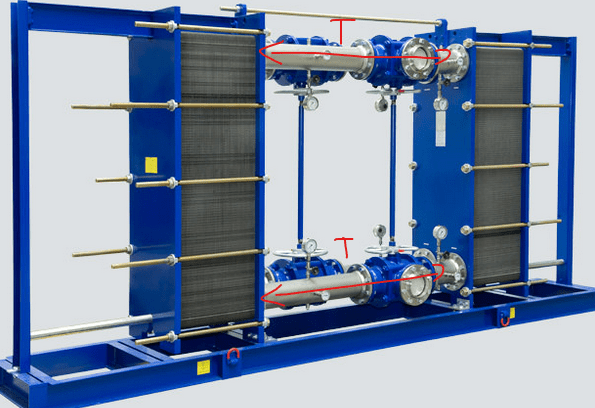
I assume that obtaining nozzle stiffness values from the manufacturer will not be an easy task, and in some cases, it may even be impossible.
...but I assume that the axial stiffness (especially of the lower cooler connections) is very high.The axial thermal forces calculated by Autopipe on these connections will be enormous, and it may be impossible to meet for e.g. the API standard.
As I mentioned above, systems of this type operate in many installations wihout damage or failure. I am wondering how to prepare a nozzles load analysis in a way that will allow to meet the standard e.g. API 662.
Regards
Marcin Wysocki