I'm trying to analyse stresse in a metalic tube, which is held in place by a flat bottom lock screw (See figure). In the study, R will remain constant, L is a constant length, and r will vary. We will assume no friction, smooth surface, isotropic linearly elastic material with σy representing the yield stress. The study will investigate the required compressive force (F) at σy.
I've tried to find a general solution to this problem, but so far it has evaded me. I've also been trying to perform and FEA through ANSYS, however my experience with ANSYS is limited, and I find this non-linear contact problem is not trivial, and I can't seem to get the solution to converge.
Could anyone assist me in tackling this problem either with ANSYS or arithmetically?
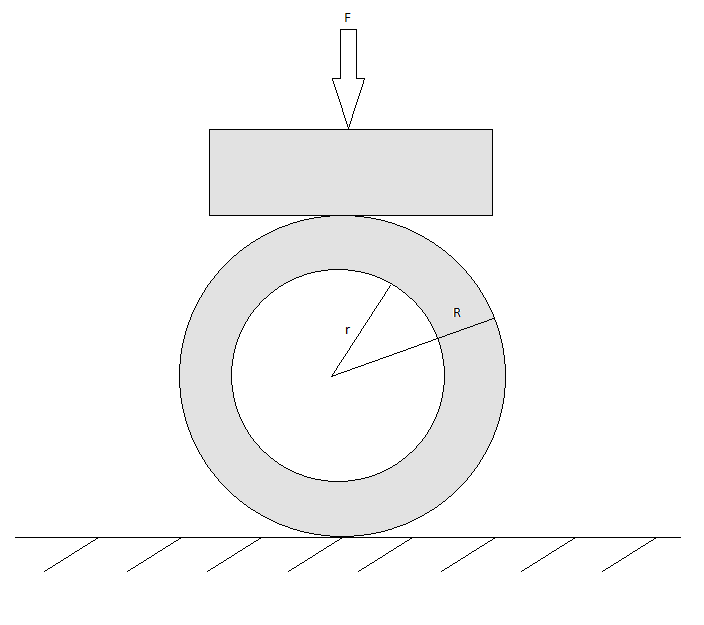
I've tried to find a general solution to this problem, but so far it has evaded me. I've also been trying to perform and FEA through ANSYS, however my experience with ANSYS is limited, and I find this non-linear contact problem is not trivial, and I can't seem to get the solution to converge.
Could anyone assist me in tackling this problem either with ANSYS or arithmetically?