Calvin Murphy
Aerospace
- Nov 22, 2024
- 16
I am hoping to settle a debate between two engineers.
I have created a simple diagram of the part of the structure we are investigating.
It can be solved in 5 minutes or less by anyone familiar with static equilibrium problems.
The goal is simple enough: find Fn.
Yet, the discussion over whose solution was correct is still unresolved. I build a rig to physically measure it, but the disagreement persisted. Then I reached out to 5 university professors to see if they would help, but I have not heard a response. So here I am. Please help.
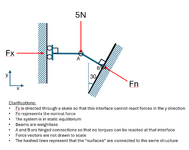
I have created a simple diagram of the part of the structure we are investigating.
It can be solved in 5 minutes or less by anyone familiar with static equilibrium problems.
The goal is simple enough: find Fn.
Yet, the discussion over whose solution was correct is still unresolved. I build a rig to physically measure it, but the disagreement persisted. Then I reached out to 5 university professors to see if they would help, but I have not heard a response. So here I am. Please help.
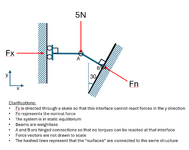