adock
Mechanical
- Nov 9, 2023
- 7
Hi all,I'm impressed by what's possible in thin wall tube forming but I'm concerned my current design isn't possible. I'm disconnected from the fabricator and I'm interested to know if this is possible before I go much further with it.
It's .039" wall, 1.5" OD, 304 SS
On the OD, I'd like to bend the tube back over itself to protect the threads (threads are formed, not shown correctly in image)
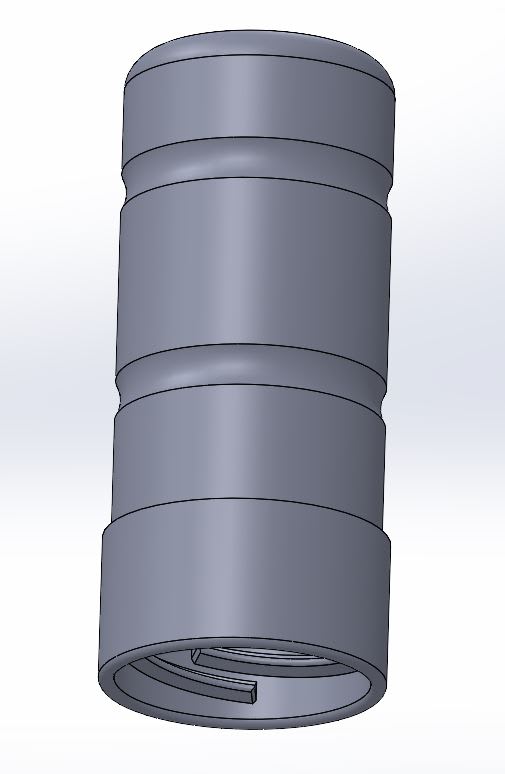
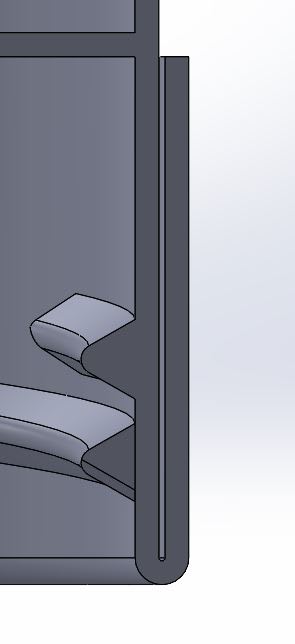