Mr_Curious
Mechanical
- Jul 14, 2020
- 47
I want to connect the walls of a groove in the rotor with screws so that the size of the groove does not change during rotation. (The groove was machined by mistake). I want to make threaded holes in the groove and screw screws into them. The threaded holes are obtained with a cutout. Have you come across in a books the calculation of a threaded connection with a cutout in the hole like mine? I am interested in how the strength calculation of these connections is carried out.
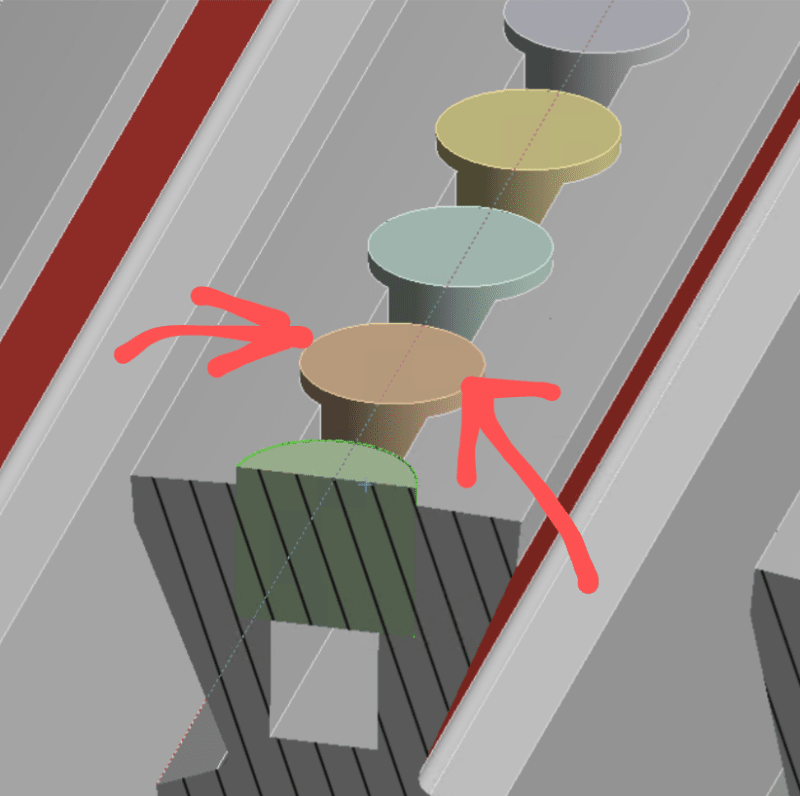