MattEdwards
Mechanical
What's the best way to apply a 'flushness' tolerance to two nominally coincident surfaces? Is there a good way of doing so without needing to specify a datum?
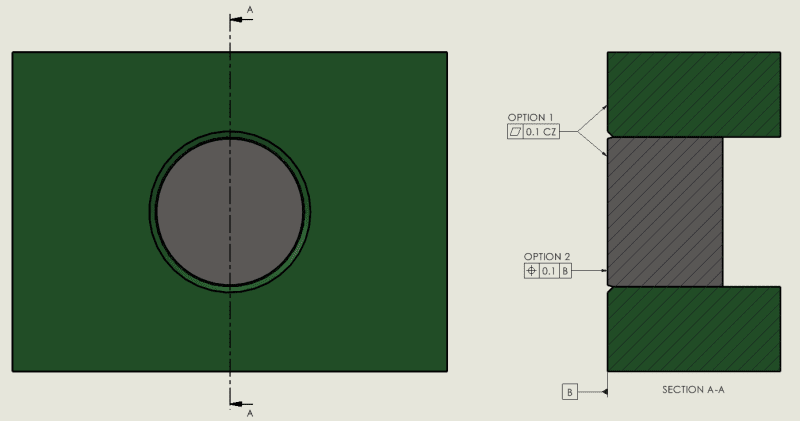
Follow along with the video below to see how to install our site as a web app on your home screen.
Note: This feature may not be available in some browsers.
MattEdwards said:Why is profile of a surface preferred?
MattEdwards said:Is there a simple alternative that doesn't require a CMM and doesn't use GD&T to specify a tolerance on coplanarity?