Hello,
I'm encountering an issue on one of my drawings similar to that shown in the picture below (see also this link:
The size tolerance on the shaft is smaller than the runout tolerance on the shaft. The link above mentions that in such a situation, total runout controls location and orientation. In that situation, is there any practical difference between total runout and position RFS? If it helps, my specific application is setting two coaxial bearing seats as datums A and B and controlling those datums with total runout referencing A-B.
I'm encountering an issue on one of my drawings similar to that shown in the picture below (see also this link:
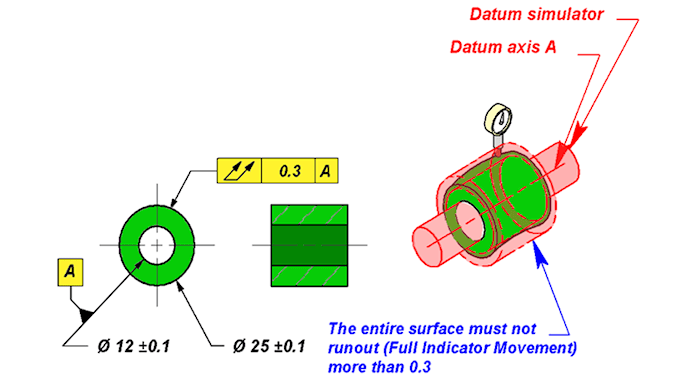
The size tolerance on the shaft is smaller than the runout tolerance on the shaft. The link above mentions that in such a situation, total runout controls location and orientation. In that situation, is there any practical difference between total runout and position RFS? If it helps, my specific application is setting two coaxial bearing seats as datums A and B and controlling those datums with total runout referencing A-B.