I'm finishing up a design for a consumer product that someone else started. Can't share the specific details unfortunately. I have a nylon part that has a 35mmx49mm footprint with a radial brim flush with the bottom that sticks out 1mm and is 4mm tall (from the bottom). All the corners have a generous radius. There is a boot that fits over the bottom of the box and over this brim. The boot is about 2mm thick and extends just over the brim (~2mm). The material of the boot specified is TPU Shore A95. I want the boot to be removable by hand but not sloppy or wiggle or any change of falling off. Currently the cavity of the boot is exactly the same dimensions as the nylon bot it goes over. Should I make the this an interference fit? If so in the radial direction, height or both? What would be a good starting point? Are there any rules of thumb or books, reading material to get up to speed on this sort of thing?
Thanks,
Adam
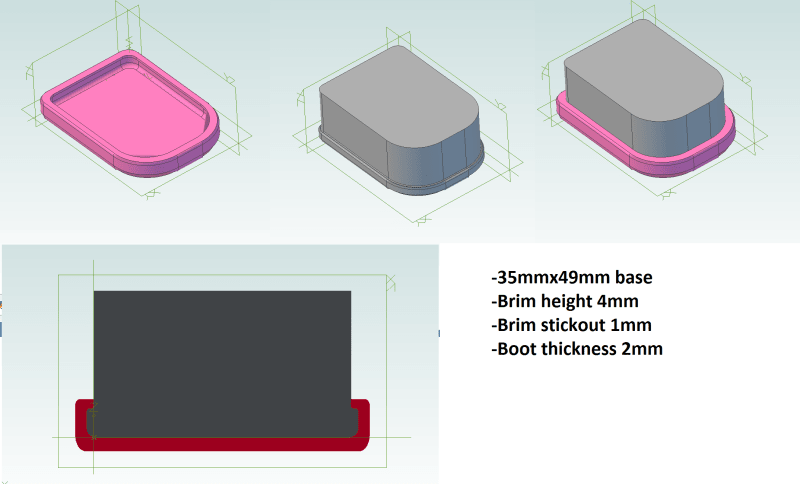
Thanks,
Adam