Mallon
Mechanical
- Nov 4, 2010
- 4
I am after some help on the design of a trolley. We are buying out a standard trolley which can hold up to 500kg. Weight of the trolley is 114. The load the trolley will be carrying is 410kg.
I have attached a picture below. As you can see the load is quite tall. We have worked out the Centre of gravity using manufactured models of the valve/chute.
The chute is connected to the valve. The trolley will be wheeled in and fastened to the underside of the valve using bolts so the load is fixed.
Can anyone give me a hand on calculating the force required to topple the trolley. The trolley will only be moving a very short distance at walking speed.
I have attached a picture below. As you can see the load is quite tall. We have worked out the Centre of gravity using manufactured models of the valve/chute.
The chute is connected to the valve. The trolley will be wheeled in and fastened to the underside of the valve using bolts so the load is fixed.
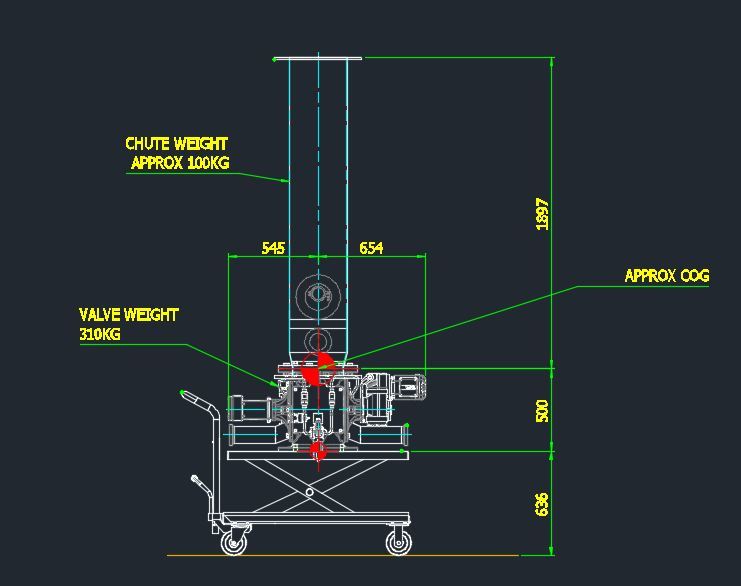
Can anyone give me a hand on calculating the force required to topple the trolley. The trolley will only be moving a very short distance at walking speed.