met33
Materials
- Apr 9, 2024
- 29
I have a couple of questions about truss blocks (aka drag blocks or shear blocks). This is my first time doing them, and they are uncommon in my area. The blocks will go between roof trusses above the exterior wall of a single-family home, adjacent to a porch overhang.
1) Is it advisable to order the truss blocks slightly undersized (e.g., 1/8" less wide and 1/4" less tall) than the nominal dimensions of the opening in which they will be installed? To prevent the roof truss spacing from "growing" horizontally due to tolerance stacking, and to ensure that the roof sheathing can lay flat above them, in case the adjacent trusses are slightly shorter than their nominal dimensions.
2) Does anyone have experience with alternate connection methods, other than A34 or A35 framing angles, which I assume are most common? I'm considering SDWS framing screws in a face screwed or toenail configuration for connecting the truss block verticals to the adjacent roof truss webs, and SDWC truss screws for connecting the bottom horizontal of the blocks to the wall top plates.
Below is an example of a truss and its corresponding truss block. Some other areas of the roof near hips have shorter blocks.
Below is a relevant detail from Mitek:
1) Is it advisable to order the truss blocks slightly undersized (e.g., 1/8" less wide and 1/4" less tall) than the nominal dimensions of the opening in which they will be installed? To prevent the roof truss spacing from "growing" horizontally due to tolerance stacking, and to ensure that the roof sheathing can lay flat above them, in case the adjacent trusses are slightly shorter than their nominal dimensions.
2) Does anyone have experience with alternate connection methods, other than A34 or A35 framing angles, which I assume are most common? I'm considering SDWS framing screws in a face screwed or toenail configuration for connecting the truss block verticals to the adjacent roof truss webs, and SDWC truss screws for connecting the bottom horizontal of the blocks to the wall top plates.
Below is an example of a truss and its corresponding truss block. Some other areas of the roof near hips have shorter blocks.
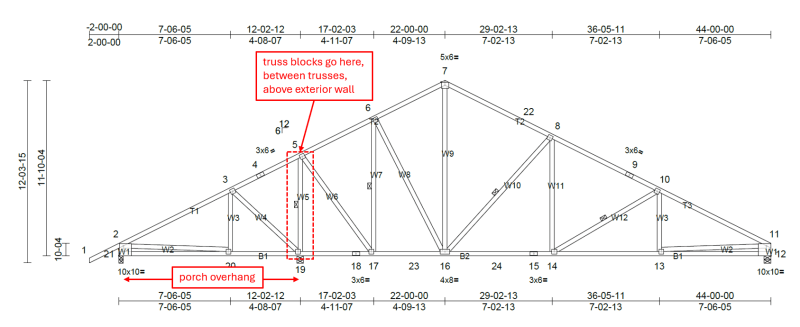
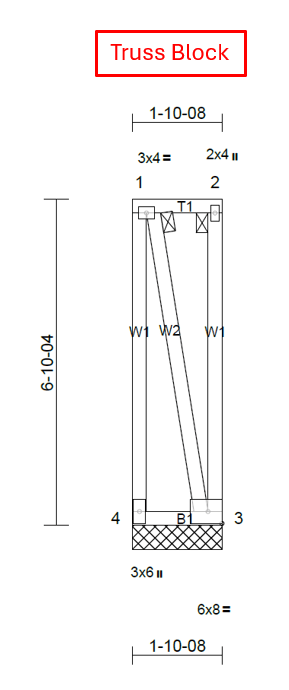
Below is a relevant detail from Mitek:
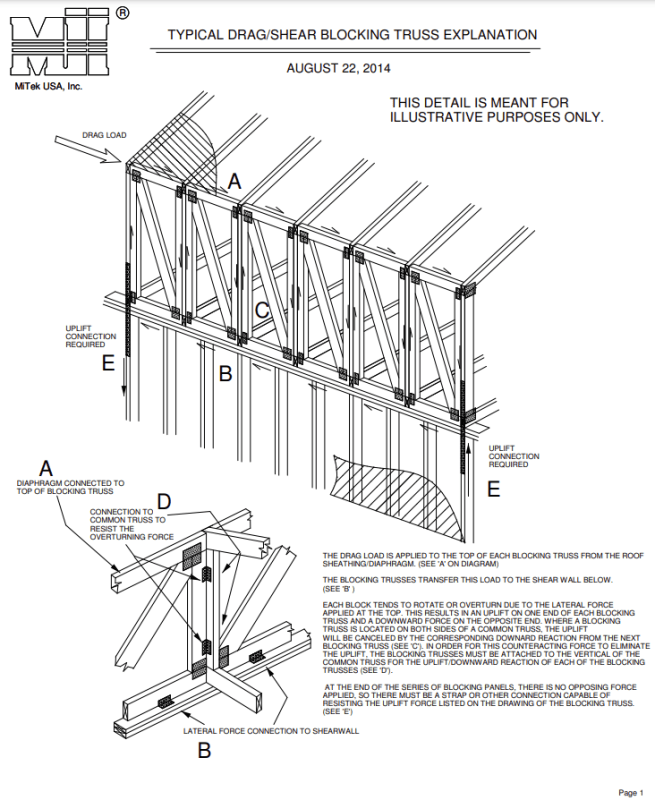