nivoo_boss
Structural
- Jul 15, 2021
- 132
Hey everyone!
So I'm designing a factory that has a vibrating equipment on one floor. The load is given like this:
Do you have any thoughts what that "6 pol" might mean?
I'm not too familiar with dynamic analysis but am trying to educate myself a little in Robot Structural Analysis.
So I'm designing a factory that has a vibrating equipment on one floor. The load is given like this:
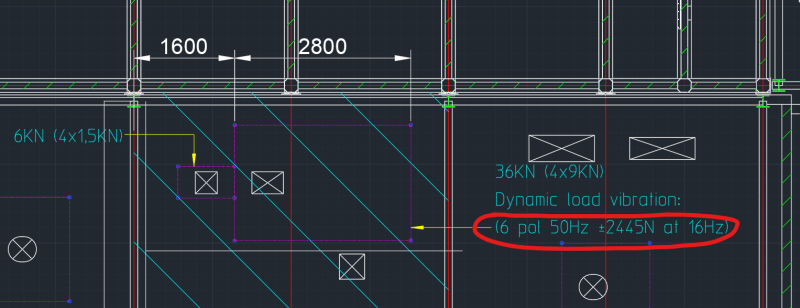
Do you have any thoughts what that "6 pol" might mean?
I'm not too familiar with dynamic analysis but am trying to educate myself a little in Robot Structural Analysis.