Hello,
I saw for the first time an engineering department in which the drawings contain a remark "Uniform Thickness XXX".
Here is an example for making it clear:
I never saw a similar comment and I would like to know if it complies with the ISO Standard (or even any other standard).
I thought that maybe an alternative form is using the profile control of both surfaces and the eccentricity of the inner/outer spheric surfaces.
I think that the UNIFORM THICKNESS = Outer_Surface_Profile + Inner_Surface_Profile + Centers eccentricity limitation
Here is an example of an alternative form of writing the same, at least in my opinion:
I saw for the first time an engineering department in which the drawings contain a remark "Uniform Thickness XXX".
Here is an example for making it clear:
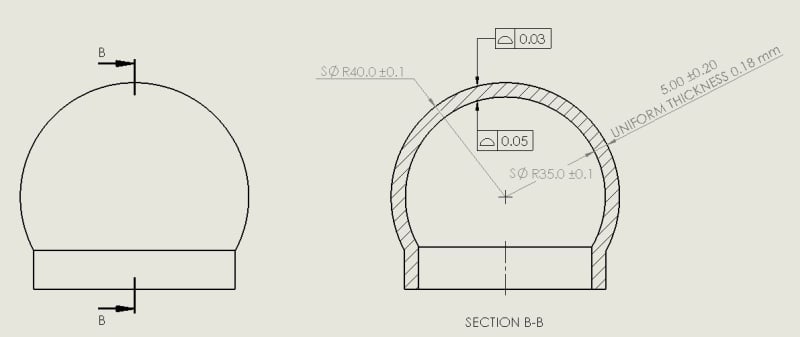
I never saw a similar comment and I would like to know if it complies with the ISO Standard (or even any other standard).
I thought that maybe an alternative form is using the profile control of both surfaces and the eccentricity of the inner/outer spheric surfaces.
I think that the UNIFORM THICKNESS = Outer_Surface_Profile + Inner_Surface_Profile + Centers eccentricity limitation
Here is an example of an alternative form of writing the same, at least in my opinion:
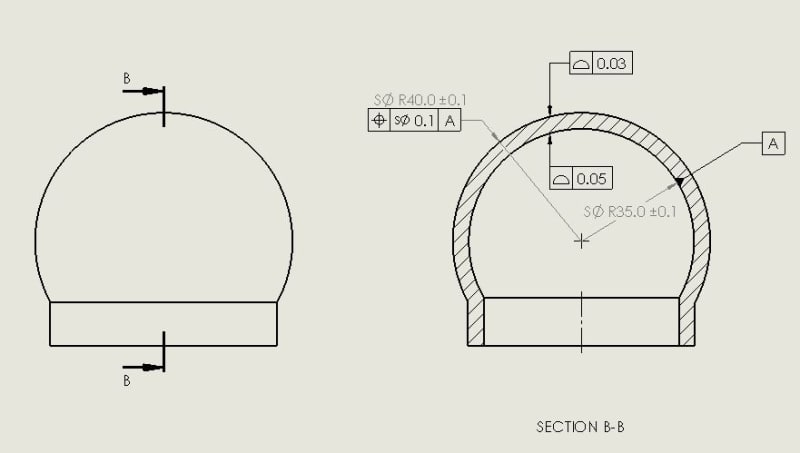