Just bought a used kiln to help with some prototype work.
Unfortunately, it is not possible to program controlled heating schedules with this kiln. It has a Kiln Sitter, which basically uses a physical piece of material (a "cone"), which softens at a certain temperature allowing a physical switch to turn off power to the kiln.
The wiring of this kiln is a bit funky, and I want to keep my modifications to a minimum.
I'm not worried about super tight temperature control. I'd like the kiln to ramp up and hold heat within a +/- 15F range at specified points.
I'd like to keep the Kiln Sitter intact as a failsafe/for future resale.
The kiln is a Skutt 145.
Could I:
- Add SSRs, control board, and thermocouple as illustrated below:
- Program the controller to open/close the relays to maintain the schedule.
Would be programmed to work something like this:
1) Set target temperature and hold time
2) Once 15 degrees above target temp is reached, open relays (cut power)
3) When temperature drops to 15F below target, close relays
4) Continue for set amount of time, and then progress to next target temperature.
5) Hold at that temperature as described in steps 2/3
6) Continue process until schedule is complete.
Thoughts? Is it bad for the elements to cycle them on/off so frequently? (I have no idea how long it would take to fall 30F, raise it back up, fall, etc,)
Unfortunately, it is not possible to program controlled heating schedules with this kiln. It has a Kiln Sitter, which basically uses a physical piece of material (a "cone"), which softens at a certain temperature allowing a physical switch to turn off power to the kiln.
The wiring of this kiln is a bit funky, and I want to keep my modifications to a minimum.
I'm not worried about super tight temperature control. I'd like the kiln to ramp up and hold heat within a +/- 15F range at specified points.
I'd like to keep the Kiln Sitter intact as a failsafe/for future resale.
The kiln is a Skutt 145.
Could I:
- Add SSRs, control board, and thermocouple as illustrated below:
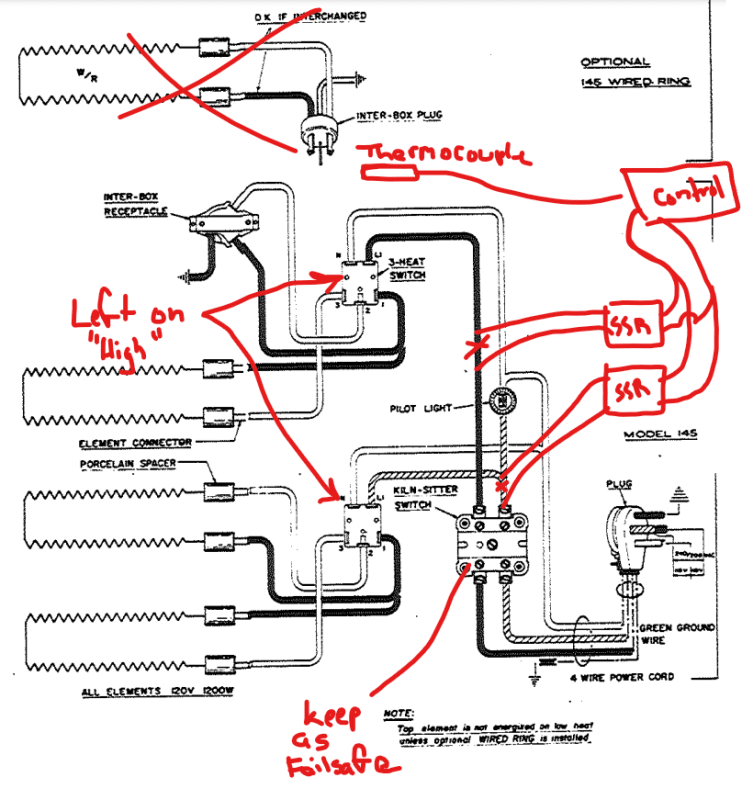
- Program the controller to open/close the relays to maintain the schedule.
Would be programmed to work something like this:
1) Set target temperature and hold time
2) Once 15 degrees above target temp is reached, open relays (cut power)
3) When temperature drops to 15F below target, close relays
4) Continue for set amount of time, and then progress to next target temperature.
5) Hold at that temperature as described in steps 2/3
6) Continue process until schedule is complete.
Thoughts? Is it bad for the elements to cycle them on/off so frequently? (I have no idea how long it would take to fall 30F, raise it back up, fall, etc,)