KootK
Structural
- Oct 16, 2001
- 18,573
I'd like to get a feel for whether or not designers of scaffold systems typically consider prefabricated, modular decking systems to have nominal diaphragm capacity. I've not been taking advantage of this to date. That said:
1) Clearly this is happening the field.
2) Clearly some engineers are doing this or, at the least, failing to recognize the problem if there is one.
3) There are situations where these diaphragms are of very small dimension perpendicular to the planks and, having stood on them myself, I can attest to their feeling quite robust even in the absence of a complete, all side vertical bracing system.
1) Clearly this is happening the field.
2) Clearly some engineers are doing this or, at the least, failing to recognize the problem if there is one.
3) There are situations where these diaphragms are of very small dimension perpendicular to the planks and, having stood on them myself, I can attest to their feeling quite robust even in the absence of a complete, all side vertical bracing system.
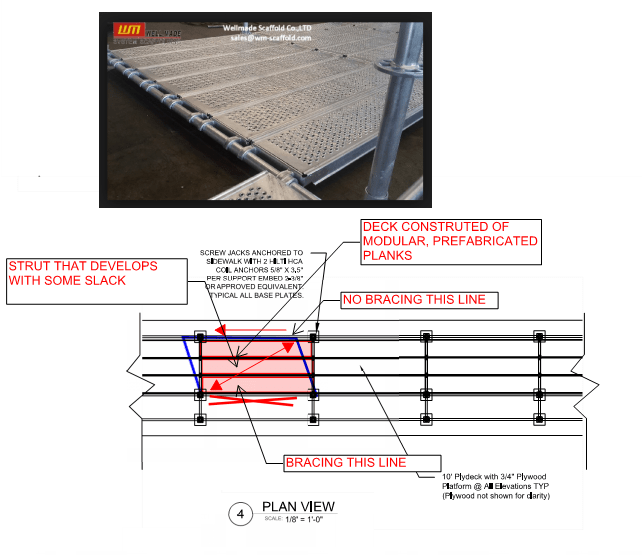