Dear All
We are operating a pump house for about 1 year. We have some maintenance issues but I can not say its numbers are abnormal.
Pump House includes:
Five pumps (each 1 MW - 60m Head) run in parallel.
The pipe is made of GRP
Fluid: Seawater 17-37 C
Recently We have received a revised stress analysis report (by CAESAR II) which depicts a very high nozzle load on the pumps (the permissible amount given by Vendor). But there is a dispute that if this analysis is right (although checked by 2 other people), based on the fact that why it has not shown any clear consequence on the pump's performance so far. Out of five pumps, we have had recently some vibration issues but they are rectified and one can associate these vibrations to causes other than high nozzle load.
In API 610, it states that pump nozzle load should be limited to ensure shaft displacement is less than 250-380 micron.
Question: Is there any way to solve our dispute by measuring the displacement of the nozzle/shaft/pipe to verify if stress analysis results are correct or not? Any method like strain gauge measurement on GRP pipe or displacement of the flange by dial indicators?
Please note that according to many references, stress analysis of GRP pipes has lots of unknowns which may result in the uncertainty of CAESAR II outputs, and this makes our case a bit difficult. If we had not constructed this pumphouse, then we could have changed the pipe layout/supports type with a conservative approach. But for the time being, it needs enough reason to make expensive changes and costly downtime.
Thanks in advance for your replies.
Hadi
We are operating a pump house for about 1 year. We have some maintenance issues but I can not say its numbers are abnormal.
Pump House includes:
Five pumps (each 1 MW - 60m Head) run in parallel.
The pipe is made of GRP
Fluid: Seawater 17-37 C
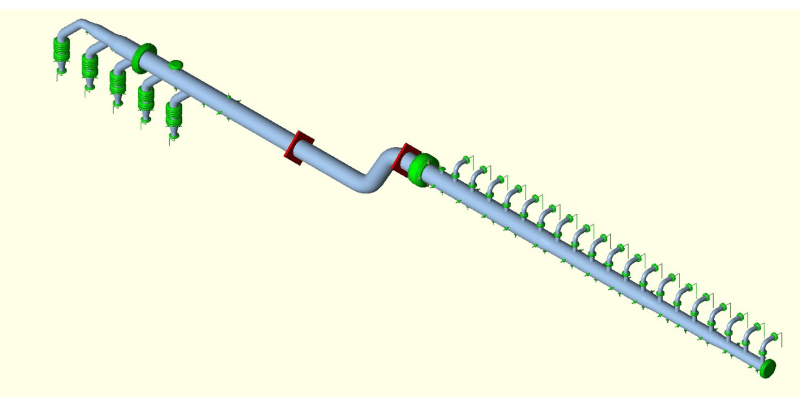
Recently We have received a revised stress analysis report (by CAESAR II) which depicts a very high nozzle load on the pumps (the permissible amount given by Vendor). But there is a dispute that if this analysis is right (although checked by 2 other people), based on the fact that why it has not shown any clear consequence on the pump's performance so far. Out of five pumps, we have had recently some vibration issues but they are rectified and one can associate these vibrations to causes other than high nozzle load.
In API 610, it states that pump nozzle load should be limited to ensure shaft displacement is less than 250-380 micron.
Question: Is there any way to solve our dispute by measuring the displacement of the nozzle/shaft/pipe to verify if stress analysis results are correct or not? Any method like strain gauge measurement on GRP pipe or displacement of the flange by dial indicators?
Please note that according to many references, stress analysis of GRP pipes has lots of unknowns which may result in the uncertainty of CAESAR II outputs, and this makes our case a bit difficult. If we had not constructed this pumphouse, then we could have changed the pipe layout/supports type with a conservative approach. But for the time being, it needs enough reason to make expensive changes and costly downtime.
Thanks in advance for your replies.
Hadi