Engineers. Salutes to all of you out there!
I have a question. I am modeling a circular base plate for an HSS round in the IDEA STATICA program. It's an 8 floors structure. The results show that a thickness of 5mm or 0.2in is enough. Only the anchors fail, but they are close to OK (as you can see in attached image). Before, I used RAM CONNECTION to design the base plates, but now I am giving to opportunity to this new program. However, This is the first base plate that I got with a so low thickness. ¡¡5mm or 0.2in!! Loads 1 and 2 are similar
What could be happening? I must to check something before calculating? I appreciate your comments.
Thanks.
I have a question. I am modeling a circular base plate for an HSS round in the IDEA STATICA program. It's an 8 floors structure. The results show that a thickness of 5mm or 0.2in is enough. Only the anchors fail, but they are close to OK (as you can see in attached image). Before, I used RAM CONNECTION to design the base plates, but now I am giving to opportunity to this new program. However, This is the first base plate that I got with a so low thickness. ¡¡5mm or 0.2in!! Loads 1 and 2 are similar
What could be happening? I must to check something before calculating? I appreciate your comments.
Thanks.
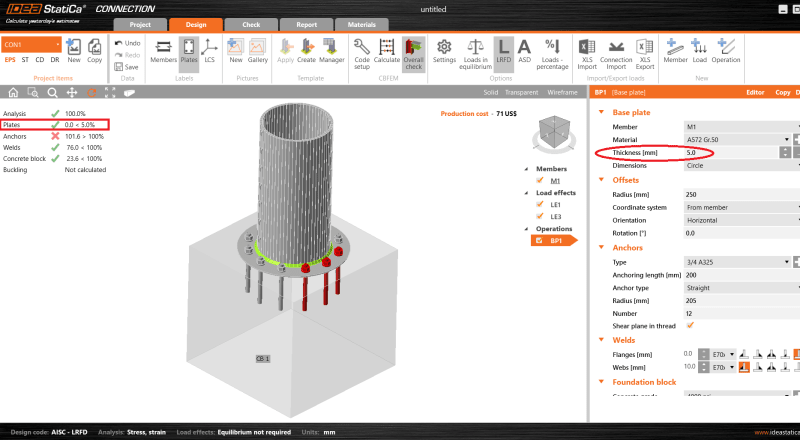
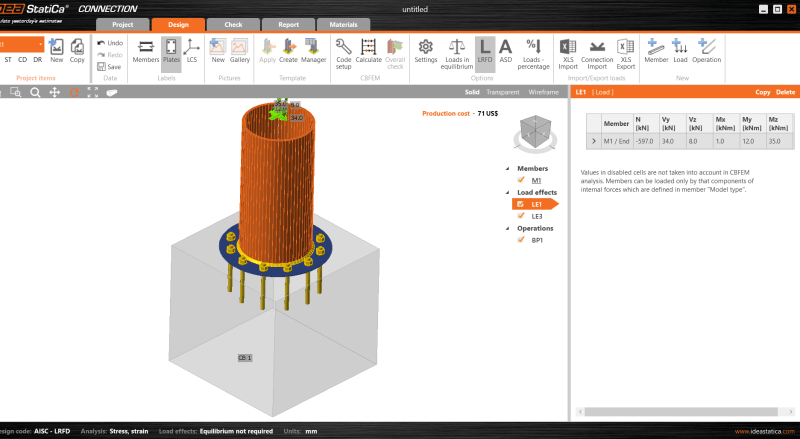