I've been tasked with creating design drawings from a vibration mitigation study performed by a specialty engineer on a composite framed steel floor with slab on metal deck for sensitive equipment. The specialty engineer used finite element modelling to determine the repairs which consist of adding posts and beams. Project is in the USA.
Beams (in red) and posts are to be added to the floor framing.
The beams parallel to the deck have us concerned. Although I'm told the FEA model took into account some orthotropic deck properties, it's strange to me that these are effective in a one way slab system. Ignoring all of this (because its not my design) we know that loads associated with vibrations are very small, such that even bolting on reinforcing is not sufficient per the literature. Reinforcing needs to be welded.
I would prefer not to discuss the effectiveness of this reinforcing layout
For those with experience, is it enough to place the beams tight to the underside of the low flutes for these to be effective? Or would they need to be engaged with the deck with a cored slab/headed stud connection?
Beams (in red) and posts are to be added to the floor framing.
The beams parallel to the deck have us concerned. Although I'm told the FEA model took into account some orthotropic deck properties, it's strange to me that these are effective in a one way slab system. Ignoring all of this (because its not my design) we know that loads associated with vibrations are very small, such that even bolting on reinforcing is not sufficient per the literature. Reinforcing needs to be welded.
I would prefer not to discuss the effectiveness of this reinforcing layout
For those with experience, is it enough to place the beams tight to the underside of the low flutes for these to be effective? Or would they need to be engaged with the deck with a cored slab/headed stud connection?
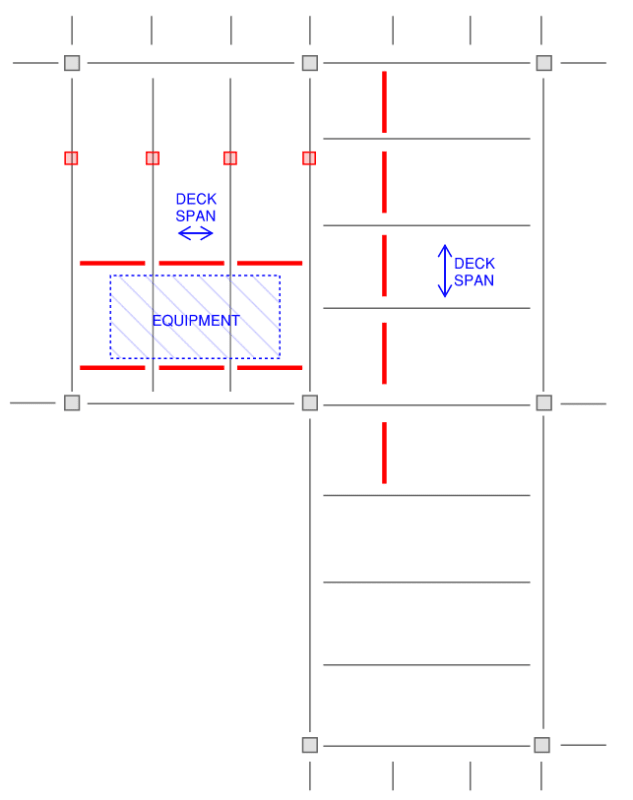