Hi all, looking for help with a dilemma I have. I’ve been asked to site weld a beam made of Rimming Steel, enclosed is the lab analysis from a sample i took.
The lab suggests adding aluminium to the weld pool to stop porosity and after looking and speaking to various technical guys I can’t get anyone to give me a straight answer of how to do it. The closest I’ve got is using E7018 rods but even still it’s a vague suggestion.
It’s not possible to take another sample before committing to the weld. The first sample was destroyed by testing.
I’d be most grateful of any advice,
Regards Nik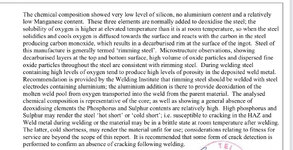
The lab suggests adding aluminium to the weld pool to stop porosity and after looking and speaking to various technical guys I can’t get anyone to give me a straight answer of how to do it. The closest I’ve got is using E7018 rods but even still it’s a vague suggestion.
It’s not possible to take another sample before committing to the weld. The first sample was destroyed by testing.
I’d be most grateful of any advice,
Regards Nik
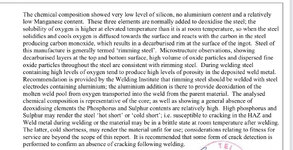