I am asked to support my team in Poland to assemble our own spreader/ lifting beam so we can transfer max of 84-ton tank/horizontal vessel. My exposure was more on industrial/ petrochem facilities but haven't used to welding thick plates.
I generally proposed CJP to connect the 50mm top and bottom lifting plates to the hot rolled beam. I practice American Code and I am familiar only with U, J or V. Im not sure what the local fabrication group proposed to us instead "Y10 a7" weld (see attached dwg). Maybe its a 10mm partial penetration groove weld with 7mm extra fillet?
I generally proposed CJP to connect the 50mm top and bottom lifting plates to the hot rolled beam. I practice American Code and I am familiar only with U, J or V. Im not sure what the local fabrication group proposed to us instead "Y10 a7" weld (see attached dwg). Maybe its a 10mm partial penetration groove weld with 7mm extra fillet?
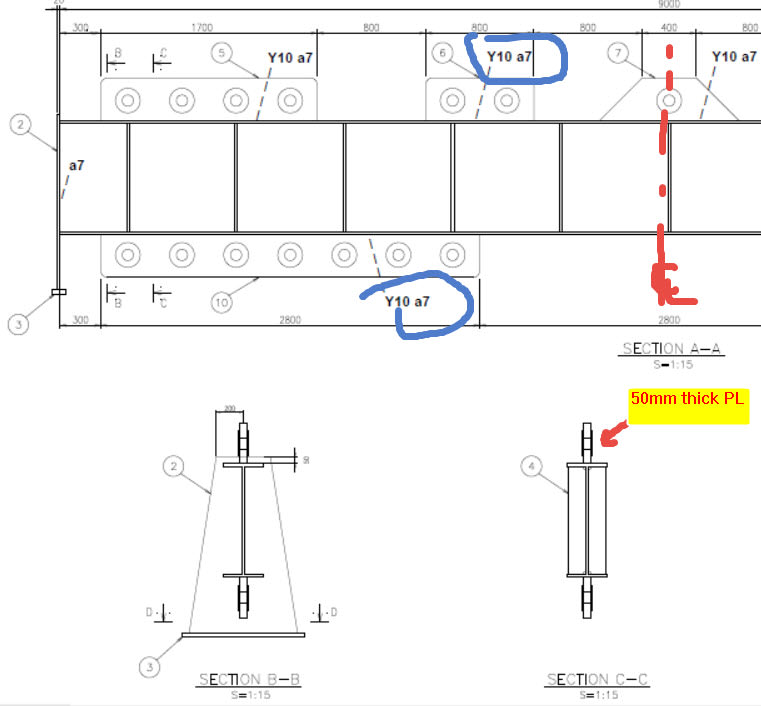