bluestar9k
Structural
The truss shown below sets on top of a 2”x4”x8’ wall with studs 16” OC; so the bottom chord is around 15’ off the ground and the truss supports are 8’ off the ground. The truss shown is one of a series of trusses set on 24” centers. The bearing wall is freestanding for 14’. Thus there are 7 trusses exerting deflection or lateral force on the freestanding wall. At the ends of the freestanding wall are lateral wall set at 90 degrees which form part of the room. The calculated lateral loads are beyond the capacity of dual 2x4 cap plate and deflections seem excessive. Shown below are 3 examples using a different combination of support connections and the resulting deflection and lateral loads.
QUESTIONS:
1. What combination of support connections should be considered for a freestanding wall?
2. How can the high lateral loads or excessive deflections be addressed?
Note: I substituted a 6”x15# wide flange as a cap plate and a lateral loading of 340# on 24” centers exceeded the capacity of a 6”x15# wide flange. Max Unity Check = [highlight #FCE94F]3.6[/highlight].
Plan View
Plan View
QUESTIONS:
1. What combination of support connections should be considered for a freestanding wall?
2. How can the high lateral loads or excessive deflections be addressed?

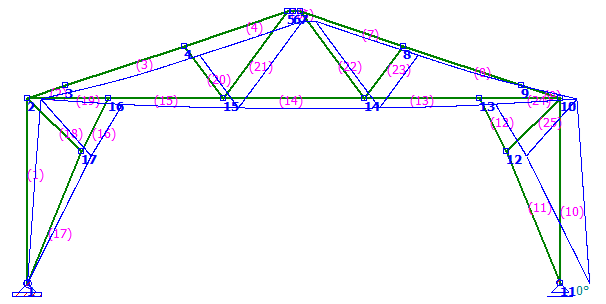

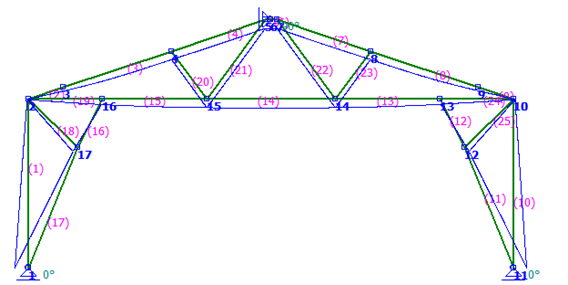

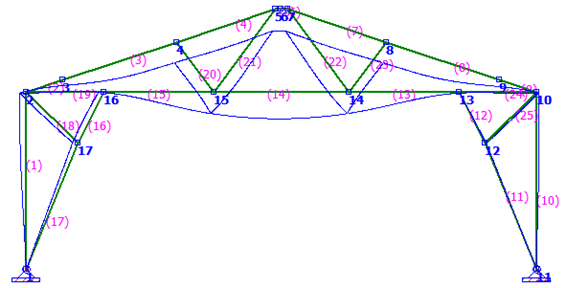
Note: I substituted a 6”x15# wide flange as a cap plate and a lateral loading of 340# on 24” centers exceeded the capacity of a 6”x15# wide flange. Max Unity Check = [highlight #FCE94F]3.6[/highlight].


Plan View

Plan View