GregLocock
Automotive
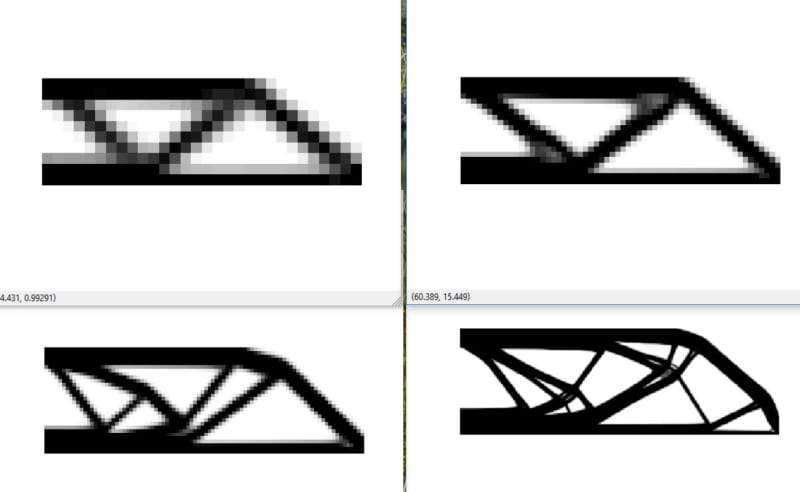
The above are 4 different runs of the amazing 99 line matlab topology optimizer. get it here . The load case is just a vertical load at the tip, all the points on the lhs are fixed. top left run is a 30x10 matrix, top right is 60x20, bottom left is 90x30, the other one is 300x100. I have not delved into the code to find out what is happening, but thought it was interesting that the design gets less sensible between the top right and bottom left, for a fairly small increment in model resolution. I am gently wondering if a better method might be to start with coarse resolution and then use that to define the solution space for the next run at finer resolution.
Cheers
Greg Locock
New here? Try reading these, they might help FAQ731-376