Good morning, I need to made an hand calculation of this component:
I verified it also with FEM, but I want to find the right theory to calculate it by hand.
1)I found the neutral line.
2)I calculate the stress on the lower and upper surface with the beam theory (but the L/H ratio is very low... can I do that?).
3)I calculate the reaction on the screws. In order to simplify the model, I removed the two central screws. The force acting on each of the 4 remaining screws is then F*340/290.
At this point, I can calculate the size of the screws needed to hold the force F.
But, how can I take into account this force on the stress of the structure?
The FEM results are very different from the calculation with beam theory, because the main stress is due to the axial force of the screws, not to the bending.
How can I take this stress into account? Membrane theory? Maybe not, the surface is too much small. Simple compression?
Thanks
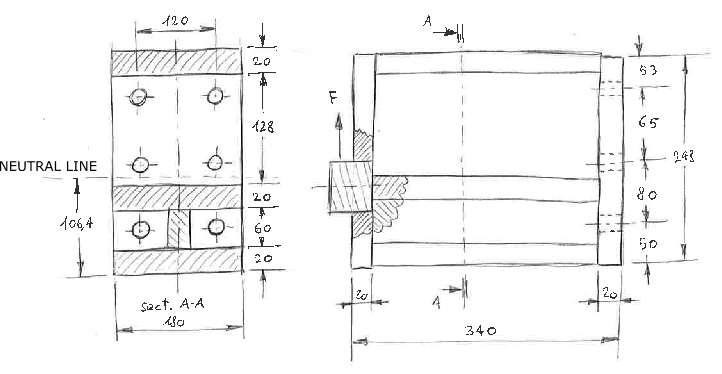
I verified it also with FEM, but I want to find the right theory to calculate it by hand.
1)I found the neutral line.
2)I calculate the stress on the lower and upper surface with the beam theory (but the L/H ratio is very low... can I do that?).
3)I calculate the reaction on the screws. In order to simplify the model, I removed the two central screws. The force acting on each of the 4 remaining screws is then F*340/290.
At this point, I can calculate the size of the screws needed to hold the force F.
But, how can I take into account this force on the stress of the structure?
The FEM results are very different from the calculation with beam theory, because the main stress is due to the axial force of the screws, not to the bending.
How can I take this stress into account? Membrane theory? Maybe not, the surface is too much small. Simple compression?
Thanks