Hello!
I am conducting a wing deflection analysis on an aircraft wing. the wing skin and spar were modelled in abaqus as separate parts. they were then assembled together using tie constraints. The ribs for the wing were defined as MPC beam constraints.
I applied a pressure load on the bottom surface of the wing skin between reference point 11 and 13 which are ribs 18 and 17. both the spar and the wing skin have been defined as shells.
The major problem I am facing is that the pressure load is acting on one concentrated part of the applied surface instead of spreading out throughout the whole wing. this is causing the wing skin to fold in like a blanket. I believe this is to do with how the wing skin is constrained to the rest of the assembly but I'm not too sure. I am working in SI units (mm, tonne/mm^3, etc).
I have included an image of what's happening. If anyone can shed light on what is happening I would greatly appreciate it. Thank you!
I am conducting a wing deflection analysis on an aircraft wing. the wing skin and spar were modelled in abaqus as separate parts. they were then assembled together using tie constraints. The ribs for the wing were defined as MPC beam constraints.
I applied a pressure load on the bottom surface of the wing skin between reference point 11 and 13 which are ribs 18 and 17. both the spar and the wing skin have been defined as shells.
The major problem I am facing is that the pressure load is acting on one concentrated part of the applied surface instead of spreading out throughout the whole wing. this is causing the wing skin to fold in like a blanket. I believe this is to do with how the wing skin is constrained to the rest of the assembly but I'm not too sure. I am working in SI units (mm, tonne/mm^3, etc).
I have included an image of what's happening. If anyone can shed light on what is happening I would greatly appreciate it. Thank you!
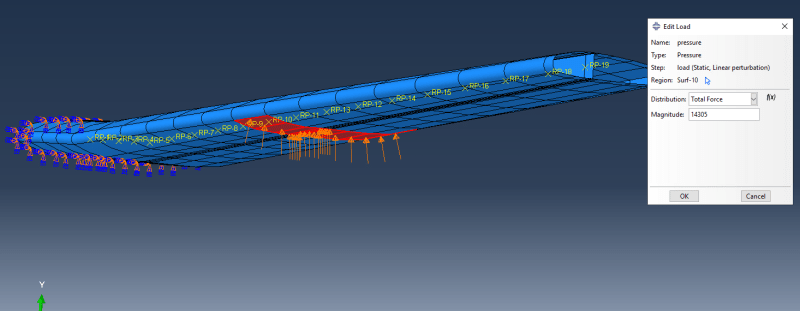
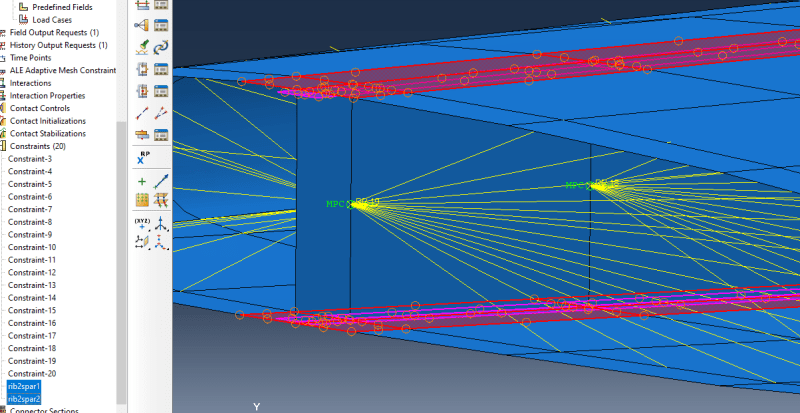
