BlasMolero
Mechanical
- Aug 12, 2009
- 928
Hello!,
I have just written a post in my blog regarding the new release of winLIFE 4.0, a fatigue analysis software integrated with FEMAP that take advanced of NX NASTRAN stress results (and from others FEM/FEA codes as well) to perform Fatigue Analysis, both uniaxial & multiaxial. The post is written in Spanish language, but you always can use the Google translator:
By means of a tutorial example I explain how to use both winLIFE 4.0 & Femap interface to perform the multiaxial fatigue analysis of a Rotating Shaft with an internal bore hole and a cross hole. A fatigue life calculation is to be carried out for this component for a rotating movement around the middle axis.
In the simulation the "trick" used was the following: instead of rotating the shaft with a fixed load, the shaft is fixed and the load rotates around the shaft. The loading of the shaft is given in angular increments, selecting an "angular window" of 90°, which results in load application angles of 0°, 90°, 180° and 270° for a unit load of 1000N. The continuous rotating movement is shown by four load cases (in real life problems the recommendation is to use a window of 30º for accuracy reasons).
Here you are the excelent quality mesh of the rotating shaft using 3-D solid hexaedral CHEXA 8-nodes elements:
Here you are the stress results for the rotating shaft at the load application angle of 0º:
And here you are the Fatigue Damage Sum results back in FEMAP for postprocessing:
And finally here you are the Utilization Ratio results back in the FEMAP model: an utilization ratio of 1.0 signifies the endurance limit is reached. A degree of utilization of 0.044 means a 4.4% usage of the endurance limit. The Utilization Ratio is the inverts of the Safety against Endurance Limit, result computed as well by winLIFE.
Best regards,
Blas.
~~~~~~~~~~~~~~~~~~~~~~
Blas Molero Hidalgo
Ingeniero Industrial
Director
IBERISA
48004 BILBAO (SPAIN)
WEB: Blog de FEMAP & NX Nastran:
I have just written a post in my blog regarding the new release of winLIFE 4.0, a fatigue analysis software integrated with FEMAP that take advanced of NX NASTRAN stress results (and from others FEM/FEA codes as well) to perform Fatigue Analysis, both uniaxial & multiaxial. The post is written in Spanish language, but you always can use the Google translator:
By means of a tutorial example I explain how to use both winLIFE 4.0 & Femap interface to perform the multiaxial fatigue analysis of a Rotating Shaft with an internal bore hole and a cross hole. A fatigue life calculation is to be carried out for this component for a rotating movement around the middle axis.
In the simulation the "trick" used was the following: instead of rotating the shaft with a fixed load, the shaft is fixed and the load rotates around the shaft. The loading of the shaft is given in angular increments, selecting an "angular window" of 90°, which results in load application angles of 0°, 90°, 180° and 270° for a unit load of 1000N. The continuous rotating movement is shown by four load cases (in real life problems the recommendation is to use a window of 30º for accuracy reasons).
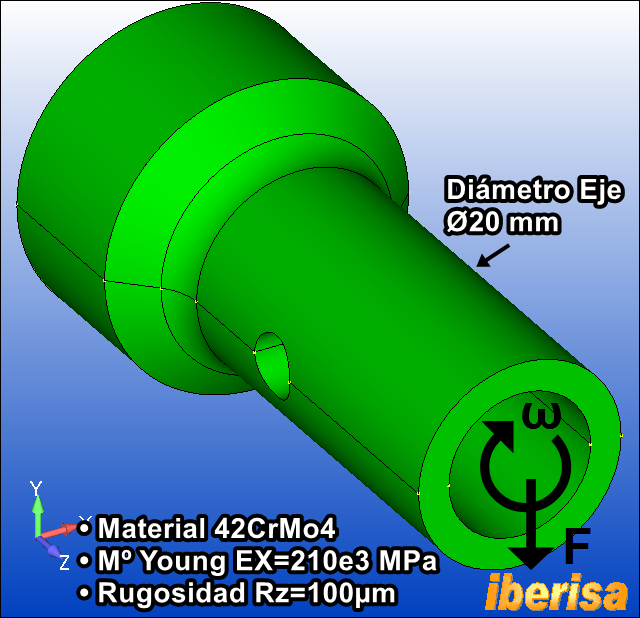
Here you are the excelent quality mesh of the rotating shaft using 3-D solid hexaedral CHEXA 8-nodes elements:
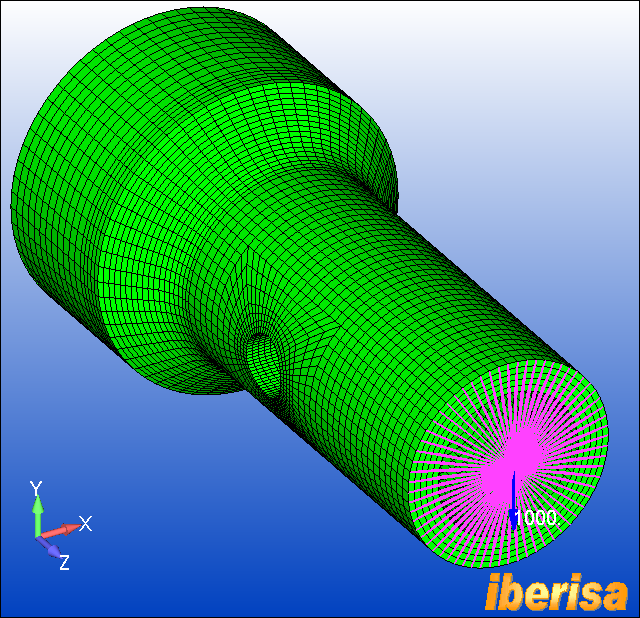
Here you are the stress results for the rotating shaft at the load application angle of 0º:
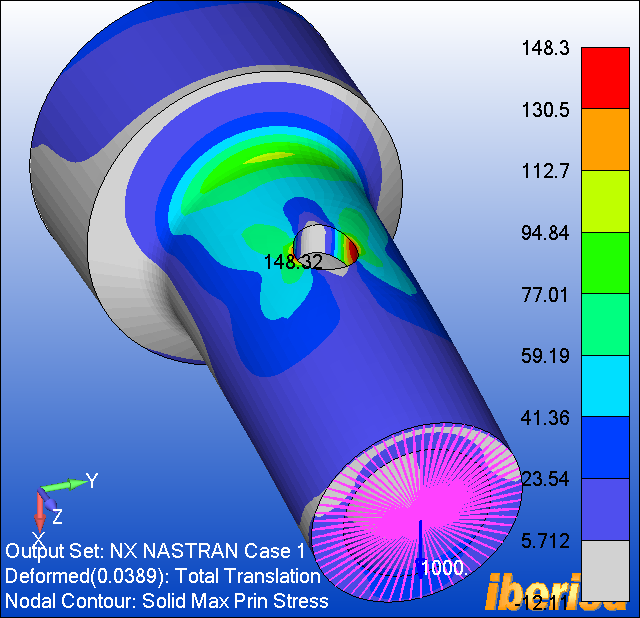
And here you are the Fatigue Damage Sum results back in FEMAP for postprocessing:
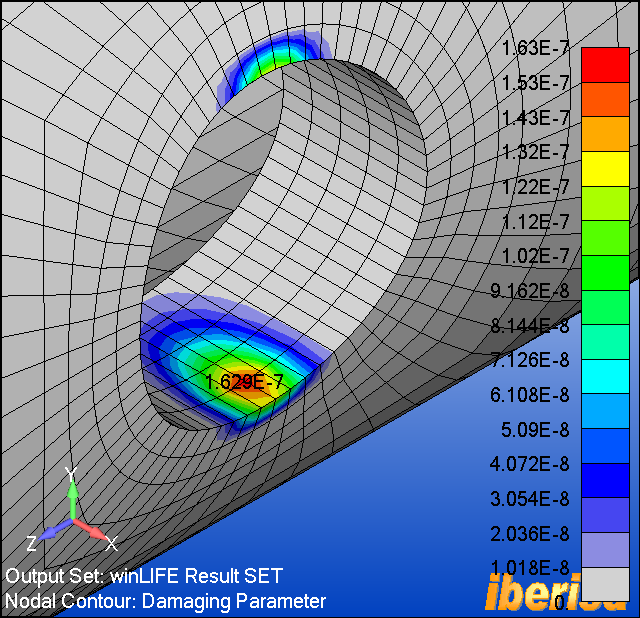
And finally here you are the Utilization Ratio results back in the FEMAP model: an utilization ratio of 1.0 signifies the endurance limit is reached. A degree of utilization of 0.044 means a 4.4% usage of the endurance limit. The Utilization Ratio is the inverts of the Safety against Endurance Limit, result computed as well by winLIFE.
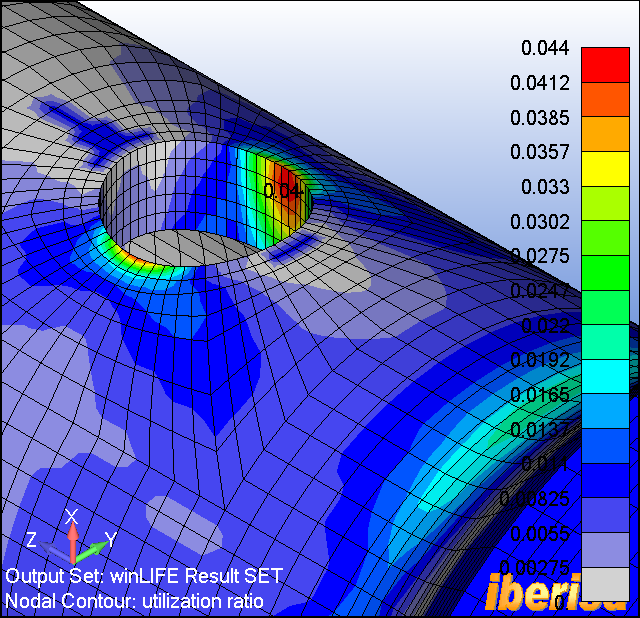
Best regards,
Blas.
~~~~~~~~~~~~~~~~~~~~~~
Blas Molero Hidalgo
Ingeniero Industrial
Director
IBERISA
48004 BILBAO (SPAIN)
WEB: Blog de FEMAP & NX Nastran: