Guastavino
Structural
All,
Forgive me as this question isn't 100% structural, but in some ways it is...
So, I'm doing a 3-story wood building (medical office). The architect wants to use 3/4" gypsum concrete over #15 asphalt felt over (2) layers of 5/8" of T&G plywood. Floor system is TJI's at 16" o/c max. The gypsum concrete and extra plywood layer is for noise control. But in thinking through this, I'm wondering where their detail came from. I asked them about it and they didn't really give a reason, just said it was for noise control. I pointed out that the APA recommends the below pictured system. They didn't really comment back. I'm curious if others have used a system like they want with the (2) layers of sheathing. It seems to me like the APA detail is better, and possibly cheaper (more gyp-crete, less sheathing). And if it was me, and an independent trade organization recommended something, I'd almost always go with it. That way, you have ground to stand on if any complaints arise. Just point out that you went with the industry standard. (This of course assumes the industry standard makes sense and works in the particular application).
Any thoughts on their detail of 3/4" gypsum concrete over #15 asphalt felt over (2) layers of 5/8" of T&G plywood as opposed to the below? I don't want to confront the architect on this without good reason. As an aside, structurally I'm only going to count one layer of sheathing for the diaphragm.
Forgive me as this question isn't 100% structural, but in some ways it is...
So, I'm doing a 3-story wood building (medical office). The architect wants to use 3/4" gypsum concrete over #15 asphalt felt over (2) layers of 5/8" of T&G plywood. Floor system is TJI's at 16" o/c max. The gypsum concrete and extra plywood layer is for noise control. But in thinking through this, I'm wondering where their detail came from. I asked them about it and they didn't really give a reason, just said it was for noise control. I pointed out that the APA recommends the below pictured system. They didn't really comment back. I'm curious if others have used a system like they want with the (2) layers of sheathing. It seems to me like the APA detail is better, and possibly cheaper (more gyp-crete, less sheathing). And if it was me, and an independent trade organization recommended something, I'd almost always go with it. That way, you have ground to stand on if any complaints arise. Just point out that you went with the industry standard. (This of course assumes the industry standard makes sense and works in the particular application).
Any thoughts on their detail of 3/4" gypsum concrete over #15 asphalt felt over (2) layers of 5/8" of T&G plywood as opposed to the below? I don't want to confront the architect on this without good reason. As an aside, structurally I'm only going to count one layer of sheathing for the diaphragm.
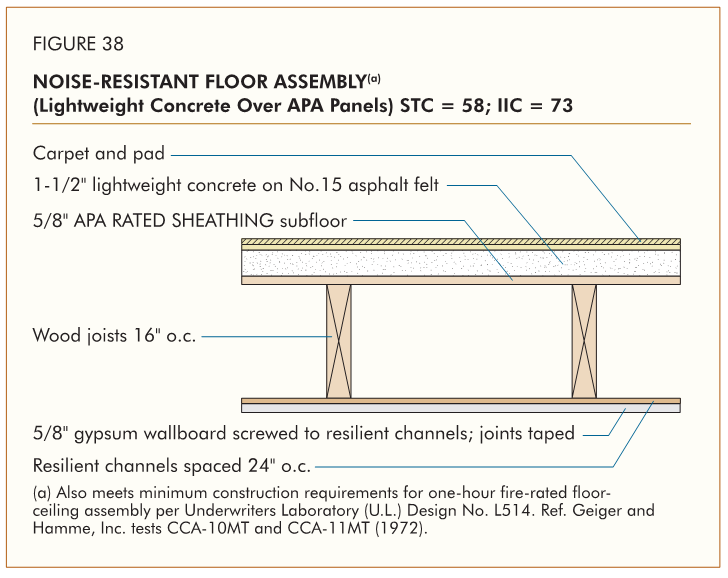