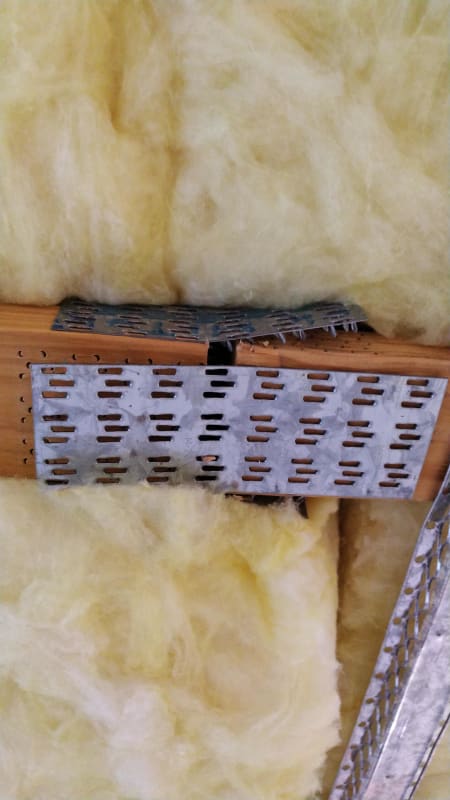
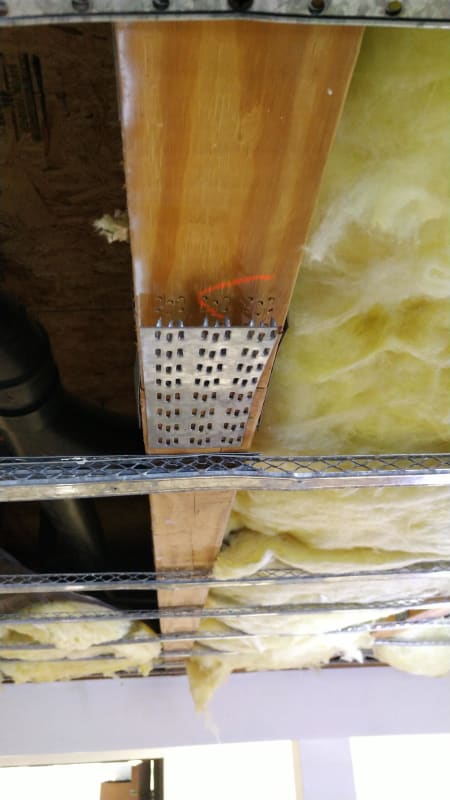
These are images wood floor trusses, taken from the floor looking up. The building is used as an assisted living facility. I cannot see how the floor would have been overloaded given the use of the facility.
Any thoughts on what could be going on? The facility was constructed in 1996. The floor live load for this area was listed at 100 psf.
I am making an additional visit to the site tomorrow to see if I can figure out what is happening. Apparently as the contractor doing cosmetic renovations removes areas of ceilings, he is finding this condition frequently.
Thanks in advance for any insight.