JungleJoe
Structural
- Jun 25, 2021
- 35
Hi everyone, thanks for reading. I am working on a residential project with a southwest-style flat roof with parapets. One area of the roof is going to be usable space with stairs going up to it on the exterior of the home. Below this area is a deck that you can walk out onto from the kitchen. I am working up a detail for the parapet wall at the usable roof space above. The owner does not want to use kickers to support the parapet for obvious reasons. Balloon framing the parapet is also not an option since it is an open deck below. The "floor" that you walk on will be 2x10's that hang into a beam that spans to a 6x6 column at each end. I want to see what your opinions are on this detail I'm working on. I am thinking that with the sheathing applied to both faces of the parapet wall and the SDS screws into the beam that this wall will be quite sturdy. There is no snow load to worry about where this home is being built. One thought I had (labeled on the drawing) for some peace of mind was to add an MST strap on the inside face of every other parapet stud, attaching the stud to the beam. I'd love to hear your thoughts. The total height from the bottom of the beam to the top of the parapet wall is to be 48". I drew a 6' tall person on the drawing for scale. The beam itself is 19.5" tall. Thanks!
Here's the drawing. I have also put a link to the drawing at the bottom of the post.
Here's the drawing. I have also put a link to the drawing at the bottom of the post.
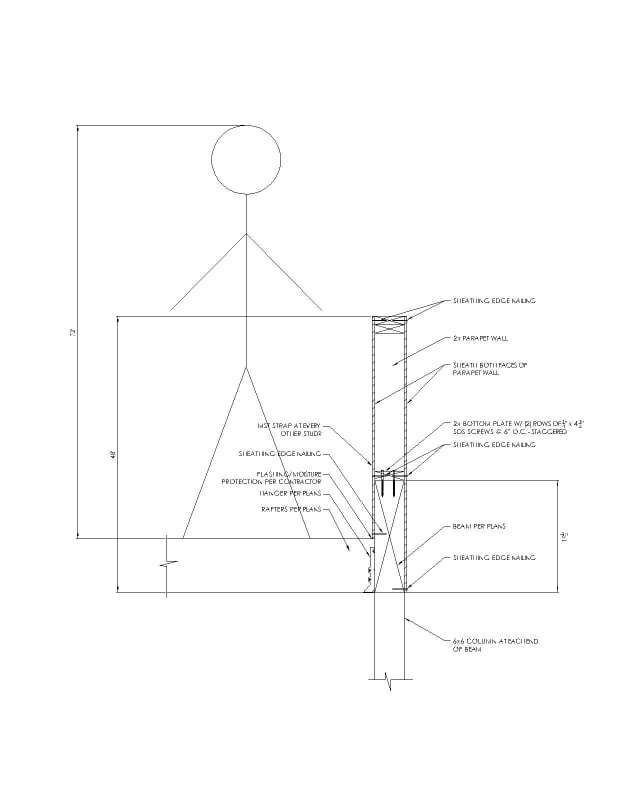