EcoGen
Structural
- Dec 8, 2020
- 59
We designed a new steel beam to replace a wall. The existing joists are to be re-attached to the steel beam per detail 5 which shows 2x infill blocking. After installing the steel beam and it's wood section infill, the Contractor has sent an RFI stating that the ends of the existing joists are too short to attach as shown in our detail. I'm guessing they trimmed the joists too short after removing the wall. I believe the joists are 2x10@16"O.C. and the beam is a W10x19.
Here are some of my thoughts on a solution:
[ol 1]
[li]Remove all of the thru bolts space at 16 in on center to remove the 2x blocking and re-install thru bolts with new 3x blocking. And make sure joists are trimmed exactly to fit. This kinda seems like an overkill since this occurs for about 60 foot of the steel beam support.[/li]
[li]Sister in joists to bridge the gap. This definitely seems like an overkill since you would probably have to sister 3 or 4 feet of the joists with a whole bunch of fasteners I imagine.[/li]
[li]Install some sort of ledger to support bottom of joists, but I'm not sure how this would look or how it would attach to our steel beam?[/li]
[/ol]
How would you re-attach ends of wood joists that are short of their support member like this?
Here are some of my thoughts on a solution:
[ol 1]
[li]Remove all of the thru bolts space at 16 in on center to remove the 2x blocking and re-install thru bolts with new 3x blocking. And make sure joists are trimmed exactly to fit. This kinda seems like an overkill since this occurs for about 60 foot of the steel beam support.[/li]
[li]Sister in joists to bridge the gap. This definitely seems like an overkill since you would probably have to sister 3 or 4 feet of the joists with a whole bunch of fasteners I imagine.[/li]
[li]Install some sort of ledger to support bottom of joists, but I'm not sure how this would look or how it would attach to our steel beam?[/li]
[/ol]
How would you re-attach ends of wood joists that are short of their support member like this?
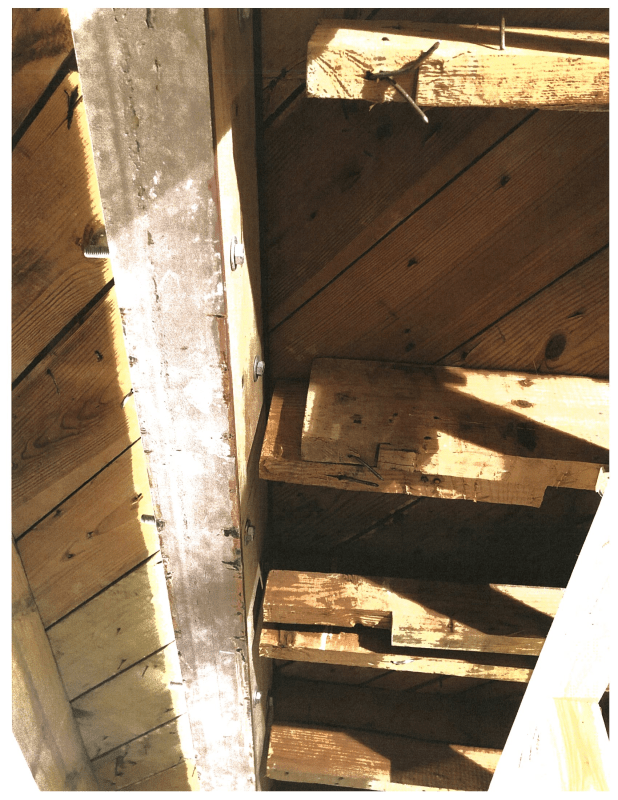
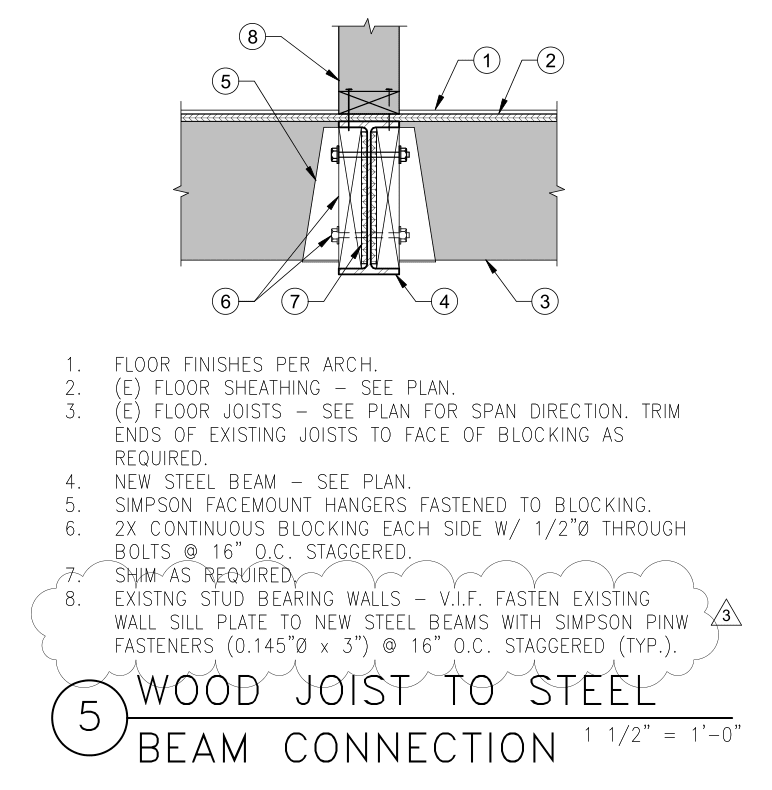