-
1
- #1
I came across the article "Evolution of the Braced Tube" by Structure Magazine that shows the 800 Fulton Market in Chicago as having an X brace with the center of the X shifted up. The article states that when the members are deflection controlled this is more efficient, but doesn't get into why. I made a model and included some screenshots from it, but am having a hard time understanding why and what shifting the node does. I'd also imagine that this significantly reduces the ductility of the structure if one of those braces buckle.
See page 46 of the June 2024 edition of the Structure Magazine.
Link
Axial forces in braces:
Deflections in all 3 braces at the top left corner of brace:
Image of 800 Fulton Market:
See page 46 of the June 2024 edition of the Structure Magazine.
Link
Axial forces in braces:
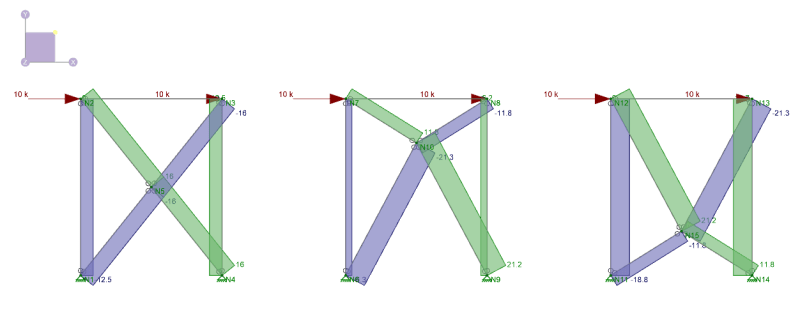
Deflections in all 3 braces at the top left corner of brace:
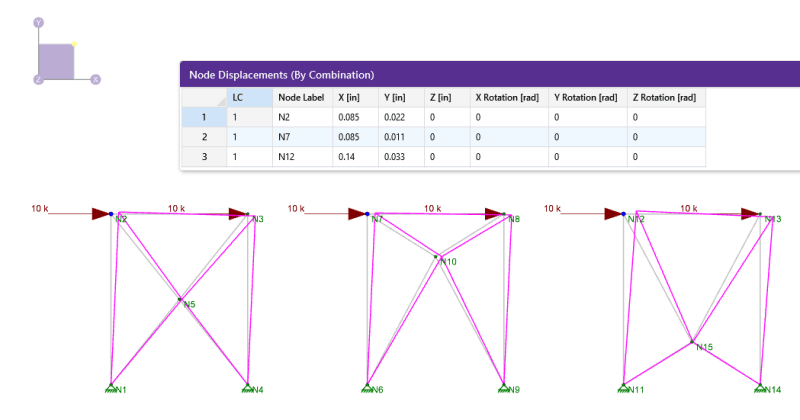
Image of 800 Fulton Market:
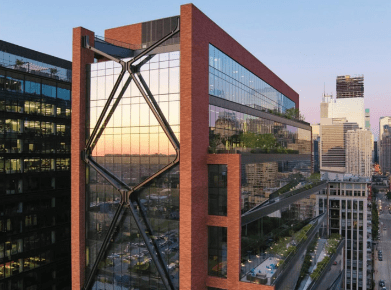