IcarusAero223
Aerospace
- Mar 10, 2024
- 10
Hi everyone! Any advice is greatly appreciated! ![[bigears] [bigears] [bigears]](/data/assets/smilies/bigears.gif)
I'm trying to model a composite test coupon damage combining LaRC05 criterion and XFEM.
To get my job converge after first element experienced some damage (STATUSXFEM between 0 and 1, usually at 0.4) I had to define damping factor of 0.0002 in the Step module (completely eyeballed this value based on some superficial reading some time ago - constant throughout the analysis).
That enabled the model to converge but ended up with an error: The system error in std_findcutshape3d8_xfem -- nodal level set values might not be correct for element 85606 instance part-1-1, its philsm are -1.85580e-02, 0.17272, -3.78320e-02, -0.20095, 8.42569e-02, -0.27117, -5.87143e-02, 0.27912.
This model had 1 enrichment zone per layer.
I tried softening displacement amplitude, refining mesh, and making enriched zone smaller and defining 2 enrichment zones per layer (above and below the hole) but nothing really helped.
Is there anything else I could try that might help my model converge better or faster? Pictures attached are the first model with the error mentioned.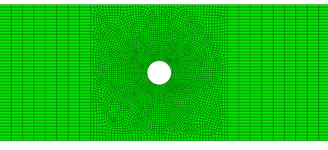
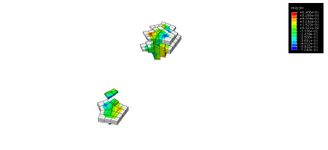
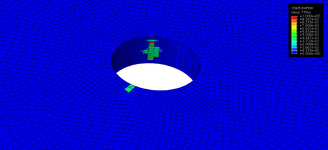
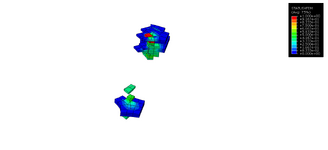
![[bigears] [bigears] [bigears]](/data/assets/smilies/bigears.gif)
I'm trying to model a composite test coupon damage combining LaRC05 criterion and XFEM.
To get my job converge after first element experienced some damage (STATUSXFEM between 0 and 1, usually at 0.4) I had to define damping factor of 0.0002 in the Step module (completely eyeballed this value based on some superficial reading some time ago - constant throughout the analysis).
That enabled the model to converge but ended up with an error: The system error in std_findcutshape3d8_xfem -- nodal level set values might not be correct for element 85606 instance part-1-1, its philsm are -1.85580e-02, 0.17272, -3.78320e-02, -0.20095, 8.42569e-02, -0.27117, -5.87143e-02, 0.27912.
This model had 1 enrichment zone per layer.
I tried softening displacement amplitude, refining mesh, and making enriched zone smaller and defining 2 enrichment zones per layer (above and below the hole) but nothing really helped.
Is there anything else I could try that might help my model converge better or faster? Pictures attached are the first model with the error mentioned.
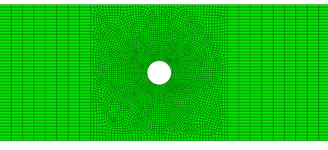
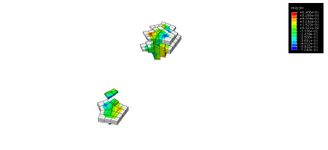
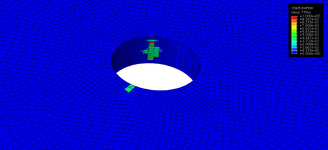
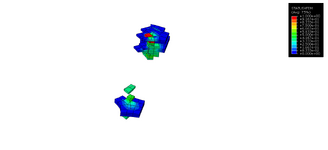