Hi y'all,
I'm not very well versed on welding and I have a question about appropriate welds for resisting tension in a direction orthogonal to the weld axis.
I am in the process of designing some brackets which will attach to a clevis and tension rod to hold up a canopy. I attached a picture for clarity -- the tension rods span from the upper lintel on the building frame to the outer end of some steel HSS members.
When I look in the Canadian steel code, there is no mention of fillet welds in tension (unless combined with partial penetration groove welds). I was hoping to create a simple design where the bottom bracket was a simple plate bent up on both ends with the 'base' welded onto the HSS. At the upper side, I would like to simply weld the brackets onto the HSS lintel. Using a plate like this would be easiest to do a fillet weld along, but as discussed I'm not sure how appropriate they are for tension (the upper bracket will be experiencing quite a lot of tension directed directly outwards from the HSS).
Does anyone with more experience have any guidance on how this could work, or a better way to approach this?
Thanks!
I'm not very well versed on welding and I have a question about appropriate welds for resisting tension in a direction orthogonal to the weld axis.
I am in the process of designing some brackets which will attach to a clevis and tension rod to hold up a canopy. I attached a picture for clarity -- the tension rods span from the upper lintel on the building frame to the outer end of some steel HSS members.
When I look in the Canadian steel code, there is no mention of fillet welds in tension (unless combined with partial penetration groove welds). I was hoping to create a simple design where the bottom bracket was a simple plate bent up on both ends with the 'base' welded onto the HSS. At the upper side, I would like to simply weld the brackets onto the HSS lintel. Using a plate like this would be easiest to do a fillet weld along, but as discussed I'm not sure how appropriate they are for tension (the upper bracket will be experiencing quite a lot of tension directed directly outwards from the HSS).
Does anyone with more experience have any guidance on how this could work, or a better way to approach this?
Thanks!
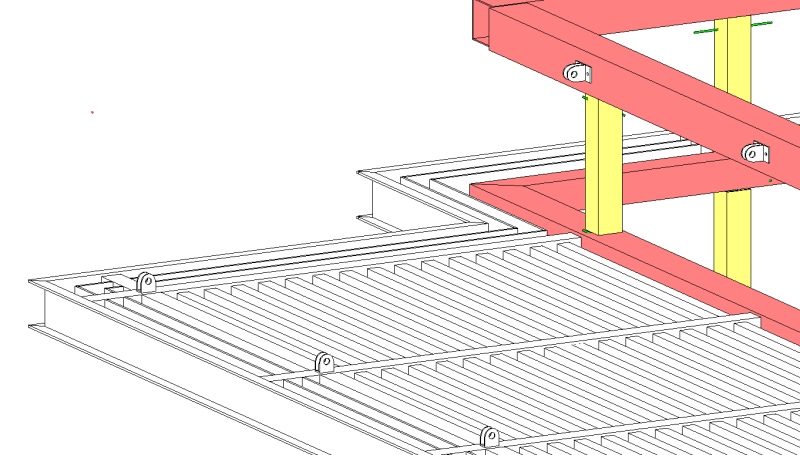