Ben29
Structural
- Aug 7, 2014
- 316
See image below. This is a pre-engineered metal building (circa 1992). I have not visited this building and I do not have the original structural drawings (not sure if I will obtain them). The picture is from the Long & Foster website. Basically I am trying to figure out if I should bid on a job that is associated with this building. It would be a heck of a lot easier if those were SJI bar joist in the picture.
Is it possible that the roof system was comprised of standard bar joist via SJI (steel joist institute)? Or is that just never done with PEMB systems? For instance, Butler currently offers this "Landmark" structural roof system which I feel is probably a proprietary truss system that looks like a bar joist.
Is it possible that the roof system was comprised of standard bar joist via SJI (steel joist institute)? Or is that just never done with PEMB systems? For instance, Butler currently offers this "Landmark" structural roof system which I feel is probably a proprietary truss system that looks like a bar joist.
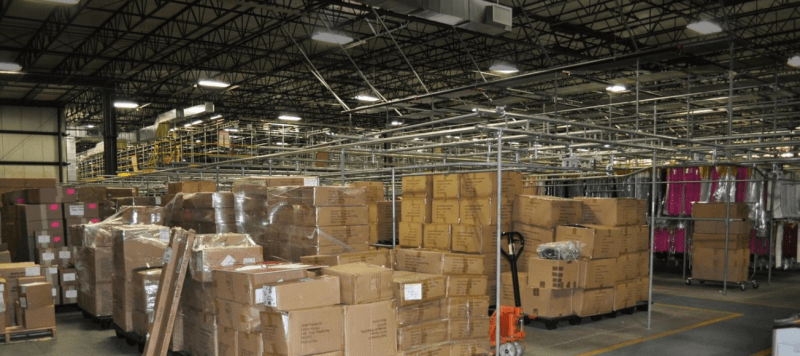