sendithard
Industrial
I'm programming this part when I had a head scratcher moment...they toleranced a +/- radius then applied an MMC zero position tolerance to it. My days of thinking/arguing over proper callouts is about exhausted so I just try to do what is best with the situation.
Internal radius is 120 deg arc(fun). The below numbers are over 10x inflated to add clarity.
Radius tolerance is 60-50mm. Position is 0 MMC A|B|C. The FCF includes a DIA symbol to is is diametrically/circular tol zone.
Our engineering team gave this only 10mm of bonus in this example...My argument is it should be 20mm of bonus. I'm explaining this first saying the radius can grow 10mm so it would take 10mm of radial movement before the mating part would intersect...therefore it is 20mm of diametrical tolerance zone.
You basically have a virtual condition envelope of 100mm in diameter that the mating part can take up. And since the part in question can be 120mm in diameter you get 20mm of bonus potential. I'm supplying the below CAD sketches...
Do you all agree that the bonus potential is 20mm?
in the pics below I'm highlighting the blue virtual condition of the mating part....then displacing the largest our feature can be left until its surface touches the virtual condition surface.
Internal radius is 120 deg arc(fun). The below numbers are over 10x inflated to add clarity.
Radius tolerance is 60-50mm. Position is 0 MMC A|B|C. The FCF includes a DIA symbol to is is diametrically/circular tol zone.
Our engineering team gave this only 10mm of bonus in this example...My argument is it should be 20mm of bonus. I'm explaining this first saying the radius can grow 10mm so it would take 10mm of radial movement before the mating part would intersect...therefore it is 20mm of diametrical tolerance zone.
You basically have a virtual condition envelope of 100mm in diameter that the mating part can take up. And since the part in question can be 120mm in diameter you get 20mm of bonus potential. I'm supplying the below CAD sketches...
Do you all agree that the bonus potential is 20mm?
in the pics below I'm highlighting the blue virtual condition of the mating part....then displacing the largest our feature can be left until its surface touches the virtual condition surface.
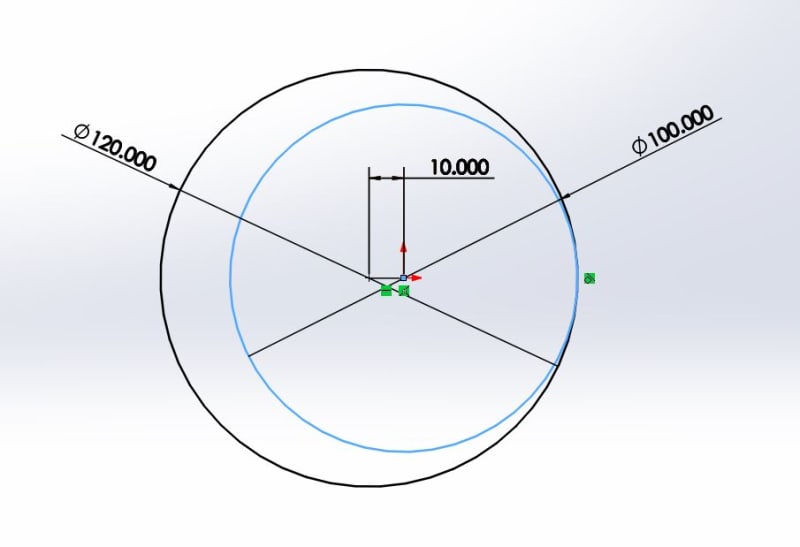
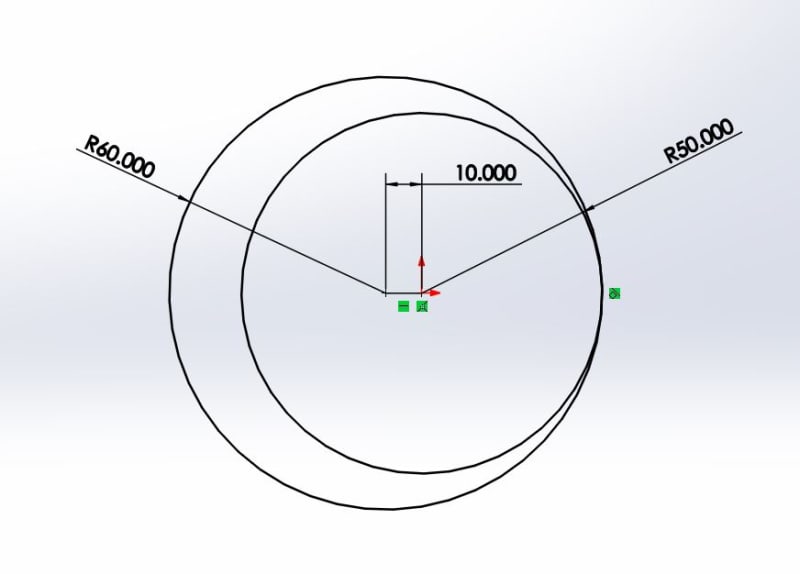