jerseyshore
Structural
- May 14, 2015
- 711
Within the last 6-12 months there has been a rush of "lifted house lifts" at the Jersey Shore. Typical house lifts are still happening at a normal pace, but because of the amount of water issues the barrier islands have now, houses that were already up 8'+ are now being raised an additional 1-3 ft. During these lifts the grade of the entire lot is getting raised up by the same amount to prevent the everyday rain/ bay water from flooding the ground floors.
Now this is typically done by cutting down the existing timber piles, installing a grade beam foundation, then building CMU/ concrete piers back up.
However, and as you can see in this picture below from a friend, engineers are signing off on timber pile splices like this now. How they justify this I have no idea and it's not something I have ever considered honestly. Seems like a waste of time to perform an analysis/ design just to find out it won't work anyway.
Most timber pile splice details I have seen are usually from DOT manuals for bridges and things of that nature.
Has anyone successfully detailed a timber pile splice like this and got it to work out on paper?
(I love the overcuts from the circle saw on the splice piece, it adds a real nice touch of craftsmanship to the entire thing)
Now this is typically done by cutting down the existing timber piles, installing a grade beam foundation, then building CMU/ concrete piers back up.
However, and as you can see in this picture below from a friend, engineers are signing off on timber pile splices like this now. How they justify this I have no idea and it's not something I have ever considered honestly. Seems like a waste of time to perform an analysis/ design just to find out it won't work anyway.
Most timber pile splice details I have seen are usually from DOT manuals for bridges and things of that nature.
Has anyone successfully detailed a timber pile splice like this and got it to work out on paper?
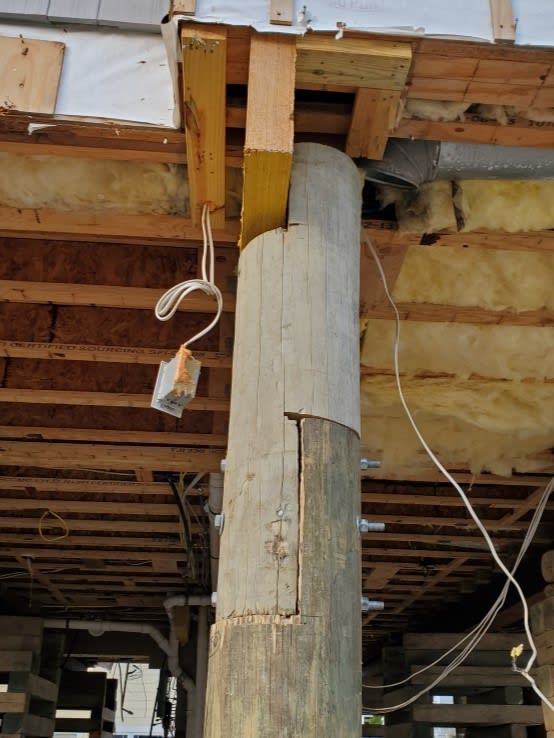
(I love the overcuts from the circle saw on the splice piece, it adds a real nice touch of craftsmanship to the entire thing)