Ingenuity
Structural
- May 17, 2001
- 2,373
I have a 5,000 lb.f capacity pull/tension hydraulic single-acting (spring return) cylinder that I need to connect to a structural steel fixture for a small scissor lift (for a 400 lb machine).
The piston rod end has a male-end with a 3/4"-14 NPT thread and the cylinder base/body has a female-end with also a 3/4"-14 NPT thread.
To connect to my steel scissor lift I am going to get some round stock and die cut 3/4"-14 NPT threads and connect to the female cylinder base, and similarly tap 3/4"-14 threads to a hole of the steel work to connect the piston rod.
3/4"-14 NPT threads have only a small engagement length - less than 1/2" - so my question is, are 3/4"-14 NPT threads structurally capable of developing my hydraulic ram tensile capacity of 5,000 lb.f?
Would have been a lot easier if the cylinder had UNC threads where I could simply use a bolt or threaded rod to make the connections.
The piston rod end has a male-end with a 3/4"-14 NPT thread and the cylinder base/body has a female-end with also a 3/4"-14 NPT thread.
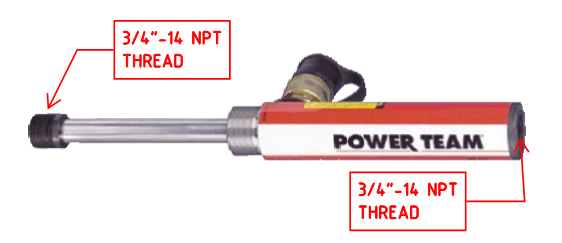
To connect to my steel scissor lift I am going to get some round stock and die cut 3/4"-14 NPT threads and connect to the female cylinder base, and similarly tap 3/4"-14 threads to a hole of the steel work to connect the piston rod.
3/4"-14 NPT threads have only a small engagement length - less than 1/2" - so my question is, are 3/4"-14 NPT threads structurally capable of developing my hydraulic ram tensile capacity of 5,000 lb.f?
Would have been a lot easier if the cylinder had UNC threads where I could simply use a bolt or threaded rod to make the connections.