novateague
Mechanical
This is a piston I had DMLS printed from AlSi10mg - the geometry is derived from generative design using some basic inputs and a starting shape. It's really just an experiment whether a consumer grade design and print can be bolted in and work for a time.
After machining, it is predicted to weigh ~50 grams vs the OEM 79 grams (1970's Honda XR75). The question is, will this lighter piston result in a small power increase as less work done by reciprocating the piston? Theoretically, the rate at which work is done will be increased?
With the reduced mass, the redline could be increased slightly due to less inertia load, but besides that? Of course, the engine should be more responsive (quicker to spin up) and with a much smaller skirt area, less friction too.
By my calculations, at maximum piston acceleration (~TDC) @ 11,000 RPM, the inertia forces on the piston are about 33% less.
After machining, it is predicted to weigh ~50 grams vs the OEM 79 grams (1970's Honda XR75). The question is, will this lighter piston result in a small power increase as less work done by reciprocating the piston? Theoretically, the rate at which work is done will be increased?
With the reduced mass, the redline could be increased slightly due to less inertia load, but besides that? Of course, the engine should be more responsive (quicker to spin up) and with a much smaller skirt area, less friction too.
By my calculations, at maximum piston acceleration (~TDC) @ 11,000 RPM, the inertia forces on the piston are about 33% less.
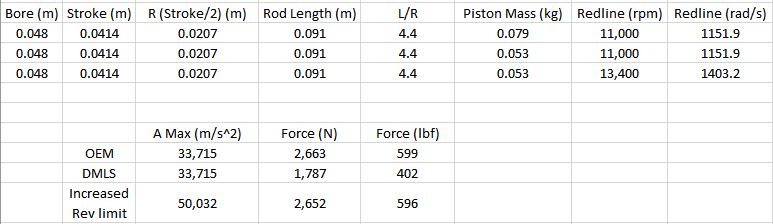

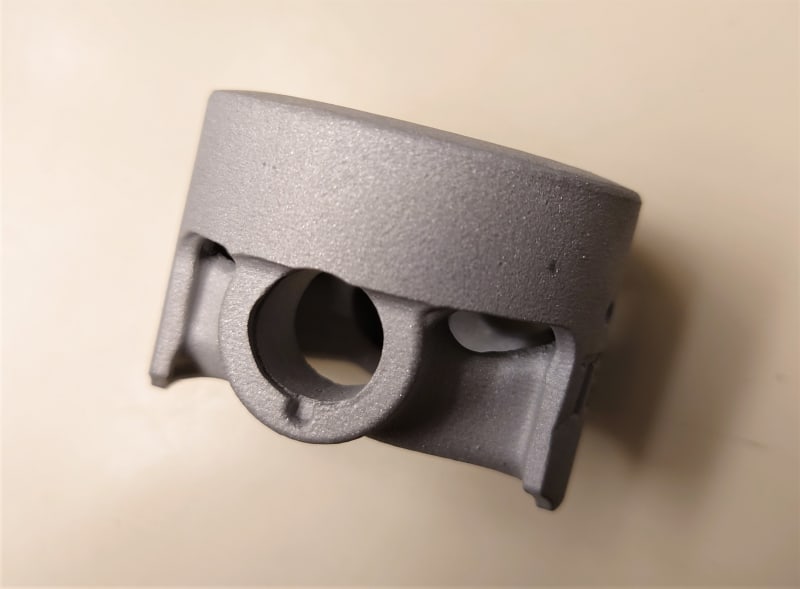
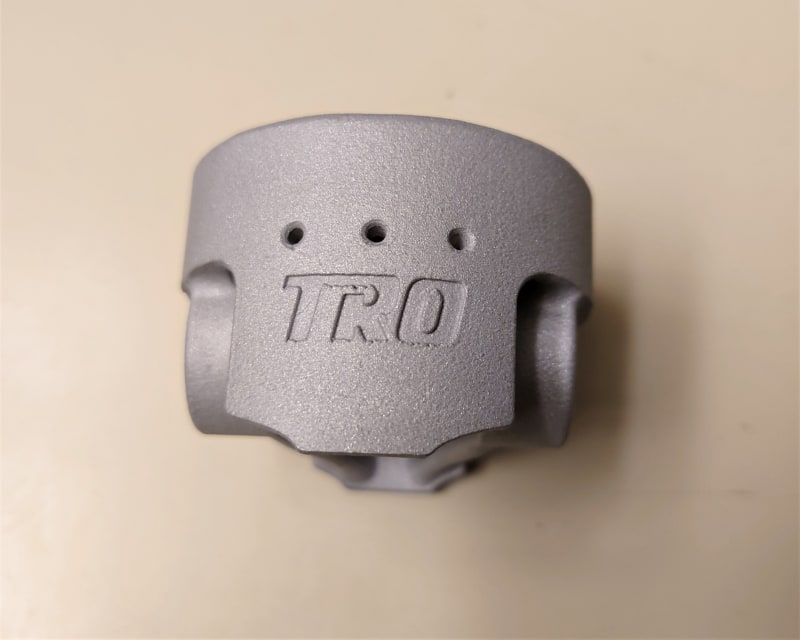