bdn2004
Electrical
- Jan 27, 2007
- 799
It's been identified that the main beam under a single story home that runs the length of the house has a hair line crack in it in the crawlspace. The crawlspace has a concrete floor. The main beam is 3 - 2 x 10s sandwiched together with 1/2" x 8" carriage bolts every three feet. The spans are about 9'-6" between piers. (Sorry about the bright flash at the bottom). We've measured a deflection of about 3/16". I hardly see any crack, and if anything it's just a hairline crack.
1. Is this crack something to concern with? When is a crack something to concern with ?
2. To shore it up and prevent it from deflecting any more we are proposing adding 2 floor jacks in between the piers. And sit each floor jack on top of a 2'x 2'x 3/4" piece of plywood.
3. Also proposing to add another 2 x 10 on one side of the main beam. What percentage extra strength would this add?
1. Is this crack something to concern with? When is a crack something to concern with ?
2. To shore it up and prevent it from deflecting any more we are proposing adding 2 floor jacks in between the piers. And sit each floor jack on top of a 2'x 2'x 3/4" piece of plywood.
3. Also proposing to add another 2 x 10 on one side of the main beam. What percentage extra strength would this add?
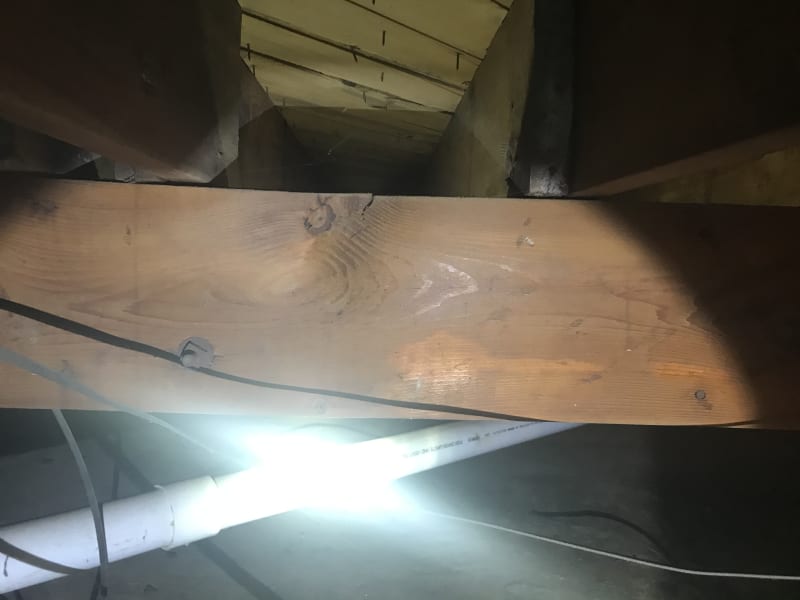