Doodler3D
Mechanical
- Jan 20, 2020
- 188
All,
I've been tasked to improve a previous experiment for a soot blowing application. Air is being fed from a 30 L tank at 8 bar. The diaphragm valve pulses for 50 ms and the goal is to measure specific impulse pressure across the tube. Since this not a steady flow application, what are the best ways to measure and quantify the drop in pressure across the pipe. The previous experiment was performed 5 years ago and the only conclusion was that the application 'worked'. I'm trying to put some numbers to the claim. A few articles online mention pressure taps at locations 2,3,4,5. The previous experiment was performed with two transducers at 1 and 6. Obviously, it did not work because of the reflections at location 6 in pressure waves the end of the pipe. The turbulence at the air exits too significantly impacts measurements. I'd appreciate a nudge in the right direction.
Thank you.
I've been tasked to improve a previous experiment for a soot blowing application. Air is being fed from a 30 L tank at 8 bar. The diaphragm valve pulses for 50 ms and the goal is to measure specific impulse pressure across the tube. Since this not a steady flow application, what are the best ways to measure and quantify the drop in pressure across the pipe. The previous experiment was performed 5 years ago and the only conclusion was that the application 'worked'. I'm trying to put some numbers to the claim. A few articles online mention pressure taps at locations 2,3,4,5. The previous experiment was performed with two transducers at 1 and 6. Obviously, it did not work because of the reflections at location 6 in pressure waves the end of the pipe. The turbulence at the air exits too significantly impacts measurements. I'd appreciate a nudge in the right direction.
Thank you.
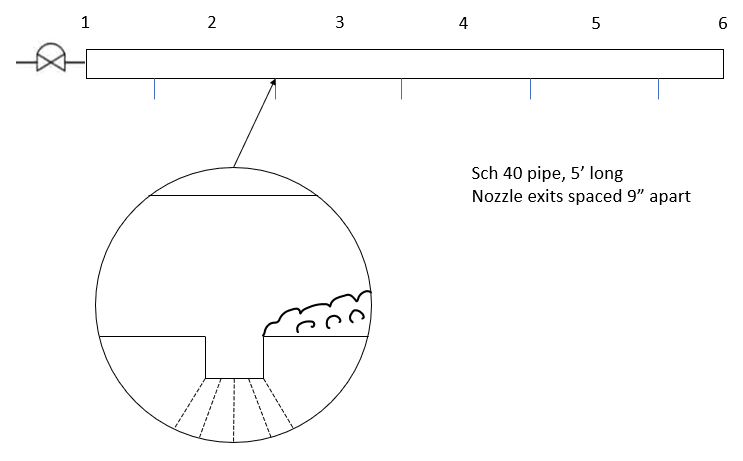