Hi
I have searched the forum but couldn't find a question quite like mine. If this has been discussed before my apologies
The closed loop consists of a tubular heat exchanger (for heating the hot water) and a plate heat exchanger (for exchanging heat to another fluid). The heat exchangers are in different locations so piping has to go up into a pipe rack and back down, and vice versa.
For a closed water loop like below, do I require both air vent valves or would 1 valve be sufficient?
Now suppose the loop has a header tank for top up and thermal relief, does this change the answer to the above?
Automatic air vent valves are a bit expensive so would probably just put a 1/2" manual valve, which can be operated periodically
Kind regards
I have searched the forum but couldn't find a question quite like mine. If this has been discussed before my apologies
The closed loop consists of a tubular heat exchanger (for heating the hot water) and a plate heat exchanger (for exchanging heat to another fluid). The heat exchangers are in different locations so piping has to go up into a pipe rack and back down, and vice versa.
For a closed water loop like below, do I require both air vent valves or would 1 valve be sufficient?
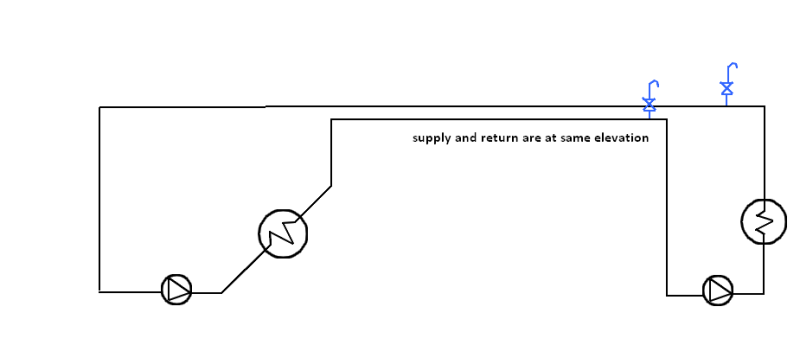
Now suppose the loop has a header tank for top up and thermal relief, does this change the answer to the above?
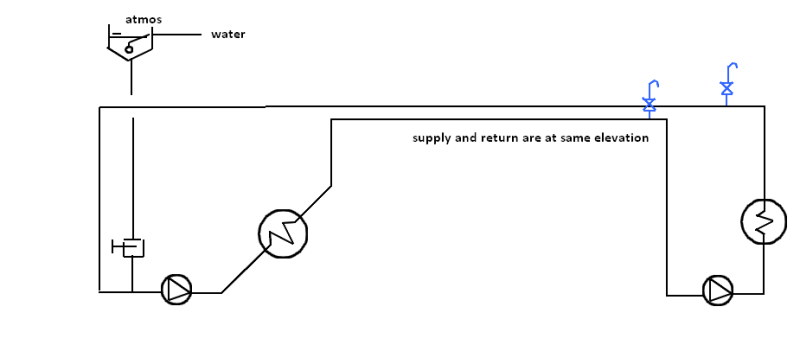
Automatic air vent valves are a bit expensive so would probably just put a 1/2" manual valve, which can be operated periodically
Kind regards