natepiercy
Mechanical
I'm very much a beginner with GD&T. My intention here is to say that the top plate must be parallel to the bottom plate (to a certain extent) and the center of the hole i the top plate must be aligned with the center of the triangle in the base plate when set on the base plate. My current struggle is that I can't find a good example of how to properly annotate the center of that equilateral triangle. Based on what I've read, a datum axis is always the product of a measurable ID or OD, so I sketched an inscribed circle in the triangle cutout on the bottom plate and put a datum target on it. Then I put a true position GTOL on the hole in the top plate, which (if I understand this correctly) says "when you set this part on datum A, the center of this feature needs to be within [dim] of datum B (the theoretical center of the triangle)". I'm looking for either affirmation that this makes sense in terms of inspection, or a suggestion for how this result should be achieved using a different method. Bonus points for references to ASME Y14.5 2009.
Thanks in advance.
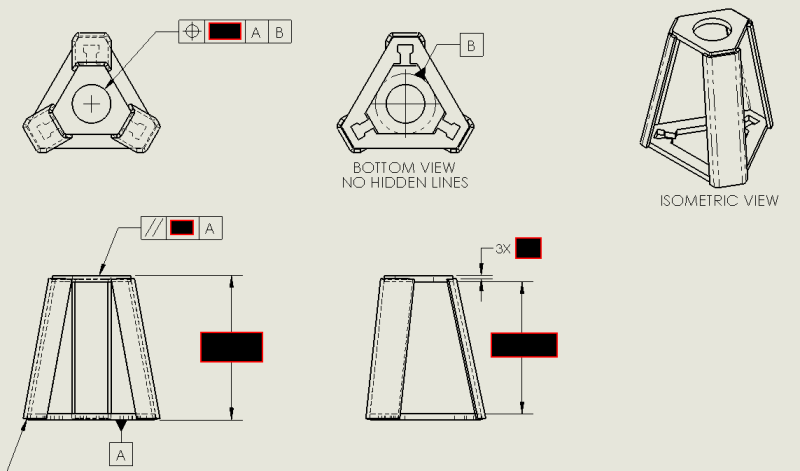
Thanks in advance.