I'm designing a chassis for a cargo trailer to be pulled by a motorcycle. It needs to be as compact as possible; there are severe limits on the thickness of the chassis, and the overall height, length, and width, and also weight, of the final trailer.
With the above in mind, the image, below, shows the first design, which consists primarily of extruded aluminium members all on the same plane. This minimises the thickness of the chassis, and thus the overall height of the trailer.
However, the problem I am having is that the design will not be strong enough, once welded, in the heat affected zones (HAZ) using standard heat treated 6000-series stock aluminium extrusions. Maintaining the geometric envelope of the chassis, and without significantly increasing its weight (such as by using a high-strength steel, which would at least double its weight), how can I mitigate the loss in yield strength in the HAZ? (I'm not talking about pre-/post-welding heating, and welding techniques to minimise the problem, as I believe they cannot prevent the significant yield strength loss I am concerned about.)I'm trying to think of ideas, but I would very much like to hear from someone with aluminium fabrication experience/knowledge as to what would be the standard solution(s), please? This is actually my first real project of the type. Pretty much, all I was taught in the classroom were the fundamentals of metallurgy, and how heat affects the strength. The easy answer (in a didactic sense) would be to fabricate the chassis, and then have it heat treated to restore its full yield strength value. However, in practise, this is awkward, and expensive (so I'm told). It makes me wonder what fabricators do to avoid the loss of strength in the HAZ, including, for example, mountains bike frame manufacturers. Perhaps, they just design-in more material in the HAZ, which is not something that would be easy to achieve for my project if I continue to use stock extrusions.
Thanks for any help.
With the above in mind, the image, below, shows the first design, which consists primarily of extruded aluminium members all on the same plane. This minimises the thickness of the chassis, and thus the overall height of the trailer.
However, the problem I am having is that the design will not be strong enough, once welded, in the heat affected zones (HAZ) using standard heat treated 6000-series stock aluminium extrusions. Maintaining the geometric envelope of the chassis, and without significantly increasing its weight (such as by using a high-strength steel, which would at least double its weight), how can I mitigate the loss in yield strength in the HAZ? (I'm not talking about pre-/post-welding heating, and welding techniques to minimise the problem, as I believe they cannot prevent the significant yield strength loss I am concerned about.)I'm trying to think of ideas, but I would very much like to hear from someone with aluminium fabrication experience/knowledge as to what would be the standard solution(s), please? This is actually my first real project of the type. Pretty much, all I was taught in the classroom were the fundamentals of metallurgy, and how heat affects the strength. The easy answer (in a didactic sense) would be to fabricate the chassis, and then have it heat treated to restore its full yield strength value. However, in practise, this is awkward, and expensive (so I'm told). It makes me wonder what fabricators do to avoid the loss of strength in the HAZ, including, for example, mountains bike frame manufacturers. Perhaps, they just design-in more material in the HAZ, which is not something that would be easy to achieve for my project if I continue to use stock extrusions.
Thanks for any help.
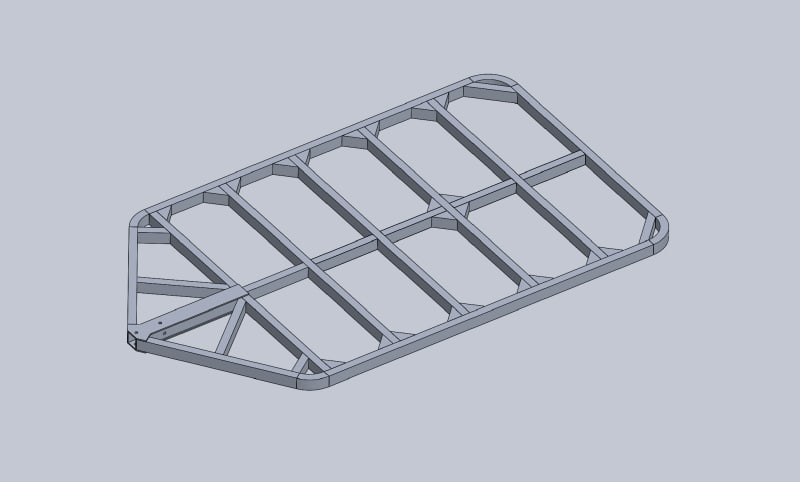