Hello,
We have an existing galvanized beam we are reinforcing partial length with cover plates and we are connecting it with bolts rather than welds.
AISC states that slip critical bolts are required to develop the force at the theoretical cutoff points but does not explicitly state SC bolts are required for shear flow.
My interpretation is that slip critical bolts are required at the ends of the cover plate but the interior bolts used for shear flow do not need to be slip critical - Agree?
We have an existing galvanized beam we are reinforcing partial length with cover plates and we are connecting it with bolts rather than welds.
AISC states that slip critical bolts are required to develop the force at the theoretical cutoff points but does not explicitly state SC bolts are required for shear flow.
My interpretation is that slip critical bolts are required at the ends of the cover plate but the interior bolts used for shear flow do not need to be slip critical - Agree?
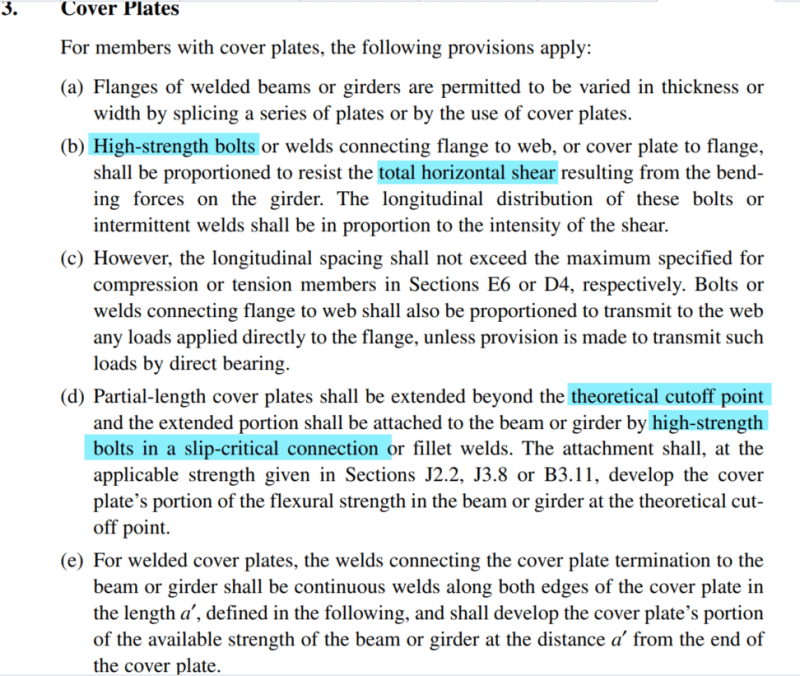