Logan82
Structural
- May 5, 2021
- 212
Hi,
I want to bolt a structure to hold a road sign board to an existing W that is part of a vehicule guardrail on the side of a bridge.
Bolts have a diameter of 5/8 in. The plate has a thickness of 3/8 in.
My client has contacted an engineer specialized in bridges, and he told him that we can't drill through the W.
The initial concept from my client was to build a custom clamp using bended plate. We would leave a gap of 1/16" between the plates so that when the bolts are torqued, they clamp the W.
However, I am having 2 issues:
- Since torquing the bolt will deform the plates just like a spring, there will be energy stored there. If the bolt breaks for some reason after a while, I am wondering if the bolt will act as a projectile.
- I can't torque the bolt a lot since the 2 plates are not in a perfect contact. I can torque approximately 10 lbf*ft, which is not alot, so I worry that the bolts may come loose. Would red loctite be sufficient to prevent bolts from coming loose?
I want to bolt a structure to hold a road sign board to an existing W that is part of a vehicule guardrail on the side of a bridge.
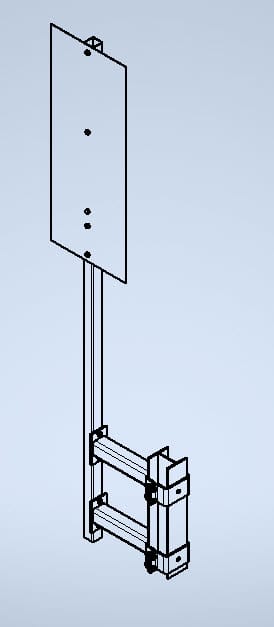
Bolts have a diameter of 5/8 in. The plate has a thickness of 3/8 in.
My client has contacted an engineer specialized in bridges, and he told him that we can't drill through the W.
The initial concept from my client was to build a custom clamp using bended plate. We would leave a gap of 1/16" between the plates so that when the bolts are torqued, they clamp the W.
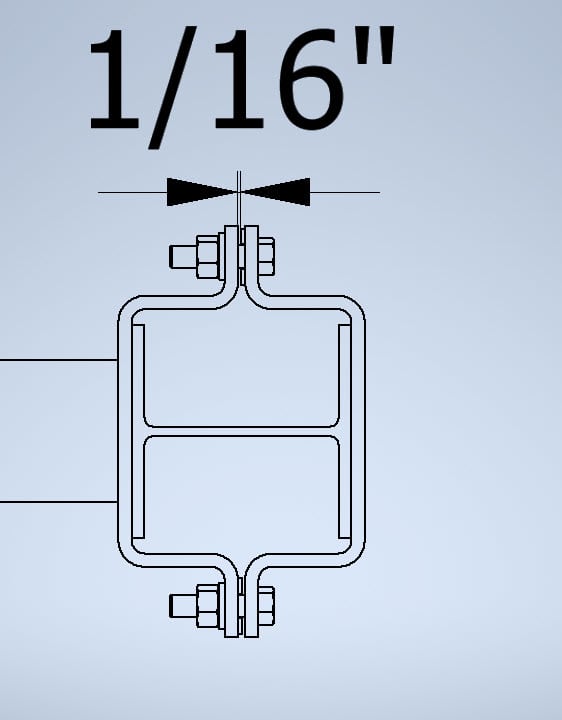
However, I am having 2 issues:
- Since torquing the bolt will deform the plates just like a spring, there will be energy stored there. If the bolt breaks for some reason after a while, I am wondering if the bolt will act as a projectile.
- I can't torque the bolt a lot since the 2 plates are not in a perfect contact. I can torque approximately 10 lbf*ft, which is not alot, so I worry that the bolts may come loose. Would red loctite be sufficient to prevent bolts from coming loose?