TiCl4
Chemical
- May 1, 2019
- 631
All,
A recent API 510 internal inspection of our pressure vessel has revealed some distressing information. The PV has a half-pipe jacket covering most of the sidewall. At some point in the past, internal pressure of the jacket exceeded MAWP by a fair margin, buckling the internal wall that is between the weldment points of the half-pipe. Not that it matters now, but I believe this was due to a PSV being installed backwards, something I noticed and had corrected several years ago. The normal process for this jacket is cooling tower water, and the inlets and outlets both close when cooling is not needed during a reaction phase. The trapped water then heats up, as it is still exposed to the hot reactor (150-200 F). Normally a thermal relief provides pressure protection, but this particular reactor was had the mis-installed thermal PRV.
Oh well. Here we are.
The "buckled" wall is uniform. Anywhere there is a half-pipe, the vessel wall is "popped in", forming a more "full pipe" jacket rather than half-jacket.
Anywhoo, the MI inspector is going to recommend the reactor be taken out of services as PV. I have asked for an FEA model of the reactor to determine if the failed state of the reactor can still retain the original MAWP and MAEP of the inner vessel and the MAWP of the jacket, essentially following an API 579 FFS review. I have read, but never seen substantiated, that half-pipe jackets provide stiffening to the shell of the vessel. ASME VIII is silent on this matter, meaning FEA must be done to prove this out.
Questions:
[ol 1]
[li]Has anyone seen FEA completed for a half-pipe jacketed reactor, specifically looking at MAEP and the benefit the jacket provides for stiffening?[/li]
[li]Looking at the picture below, does anyone have a gut feeling on what may result from an FEA analysis? The PV itself was modestly rated - approx 25 psig @ 400 F MAWP and F.V.[/li]
[li]Would this type of buckling reduce the vessel's MAWP?[/li]
[li]Unlike a full conventional jacket, which can crush a pressure vessel, it doesn't appear that the half-pipe is capable of fully collapsing a vessel. What would the failure mode be for excessive pressure in the jacket, then? The jacket alternately handles 60 psig CTW and 75 psig steam. It was originally rated at 150 psig @ 365 F.[/li]
[li]Following from the prior question, what is the main risk of continuing to run CTW or steam in the jacket? The pressure vessel normally operates at atmospheric pressure - the pressure rating is simply for emergency relief design.[/li]
[li]Non-engineering question: How screwed is this vessel?[/li]
[/ol]
A recent API 510 internal inspection of our pressure vessel has revealed some distressing information. The PV has a half-pipe jacket covering most of the sidewall. At some point in the past, internal pressure of the jacket exceeded MAWP by a fair margin, buckling the internal wall that is between the weldment points of the half-pipe. Not that it matters now, but I believe this was due to a PSV being installed backwards, something I noticed and had corrected several years ago. The normal process for this jacket is cooling tower water, and the inlets and outlets both close when cooling is not needed during a reaction phase. The trapped water then heats up, as it is still exposed to the hot reactor (150-200 F). Normally a thermal relief provides pressure protection, but this particular reactor was had the mis-installed thermal PRV.
Oh well. Here we are.
The "buckled" wall is uniform. Anywhere there is a half-pipe, the vessel wall is "popped in", forming a more "full pipe" jacket rather than half-jacket.
Anywhoo, the MI inspector is going to recommend the reactor be taken out of services as PV. I have asked for an FEA model of the reactor to determine if the failed state of the reactor can still retain the original MAWP and MAEP of the inner vessel and the MAWP of the jacket, essentially following an API 579 FFS review. I have read, but never seen substantiated, that half-pipe jackets provide stiffening to the shell of the vessel. ASME VIII is silent on this matter, meaning FEA must be done to prove this out.
Questions:
[ol 1]
[li]Has anyone seen FEA completed for a half-pipe jacketed reactor, specifically looking at MAEP and the benefit the jacket provides for stiffening?[/li]
[li]Looking at the picture below, does anyone have a gut feeling on what may result from an FEA analysis? The PV itself was modestly rated - approx 25 psig @ 400 F MAWP and F.V.[/li]
[li]Would this type of buckling reduce the vessel's MAWP?[/li]
[li]Unlike a full conventional jacket, which can crush a pressure vessel, it doesn't appear that the half-pipe is capable of fully collapsing a vessel. What would the failure mode be for excessive pressure in the jacket, then? The jacket alternately handles 60 psig CTW and 75 psig steam. It was originally rated at 150 psig @ 365 F.[/li]
[li]Following from the prior question, what is the main risk of continuing to run CTW or steam in the jacket? The pressure vessel normally operates at atmospheric pressure - the pressure rating is simply for emergency relief design.[/li]
[li]Non-engineering question: How screwed is this vessel?[/li]
[/ol]
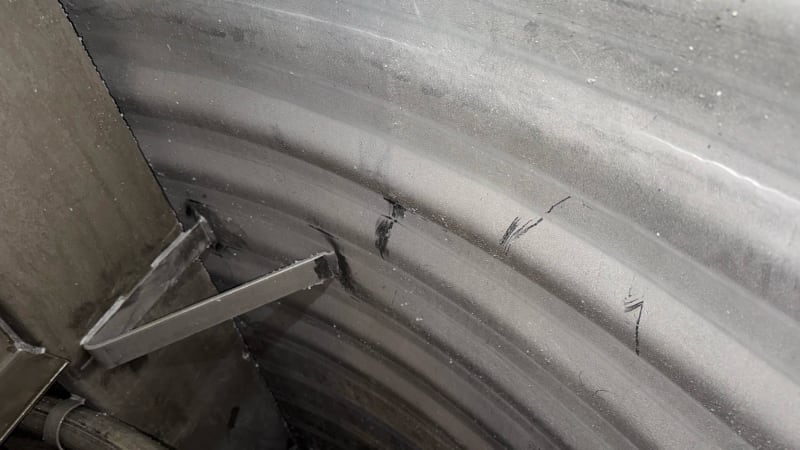